Method for preparing industrial waste alkali-resistant glass fibers modified with intermediate oxides
An alkali-resistant glass fiber and industrial waste technology, applied in glass manufacturing equipment, manufacturing tools, etc., can solve problems such as pollution, hidden dangers, land occupation safety, etc., to solve the problem of stacking pollution, simple production process, and reduce land costs The effect of occupation
- Summary
- Abstract
- Description
- Claims
- Application Information
AI Technical Summary
Problems solved by technology
Method used
Examples
Embodiment 1
[0040] A method for preparing alkali-resistant glass fibers from industrial waste modified by intermediate oxides and the prepared alkali-resistant glass fibers. The ingredients are as follows: The components and dosage are: red mud 9, blast furnace slag 21, quartz powder 52, industrial alumina 14, magnesium oxide 2.5, sodium oxide 1.5.
[0041] The experimental steps are: 1) Raw material pretreatment: Red mud is kept in a high-temperature furnace at 650°C for 170 minutes, blast furnace slag is kept in a high-temperature furnace at 310°C for 160 minutes, and then ground through a 200-mesh sieve. Other industrial raw materials are pretreated in 110°C was processed for 110 minutes to finally obtain a raw material with uniform and stable particle size and composition.
[0042] 2) Mixing: According to the ratio of raw materials, weigh each raw material and mix them evenly in a mortar.
[0043] 3) Melting: Heat the uniformly mixed batch materials in a high-temperature furnace to 1...
Embodiment 2
[0046] A method for preparing alkali-resistant glass fibers from industrial waste modified by intermediate oxides and the prepared alkali-resistant glass fibers. The ingredients are as follows: The components and dosage are: red mud 12, blast furnace slag 20, quartz powder 51, industrial alumina 13, magnesium oxide 2.6, sodium oxide 1.4.
[0047] The experimental steps are: 1) Raw material pretreatment: Red mud is kept in a high-temperature furnace at 610°C for 220 minutes, blast furnace slag is kept in a high-temperature furnace at 350°C for 180 minutes, and then ground through a 200-mesh sieve. Other industrial raw materials are pretreated in Treat at 115°C for 130 minutes to finally obtain raw materials with uniform and stable particle size and composition.
[0048] 2) Mixing: According to the ratio of raw materials, weigh each raw material and mix them evenly in a mortar.
[0049] 3) Melting: Heat the uniformly mixed batch materials in a high-temperature furnace to 1540°C...
Embodiment 3
[0052] A method for preparing alkali-resistant glass fibers from industrial waste modified by intermediate oxides and the prepared alkali-resistant glass fibers. The ingredients are as follows: The components and dosage are: red mud 15, blast furnace slag 20, quartz powder 51, industrial alumina 10.5, magnesium oxide 2.4, sodium oxide 1.1.
[0053] The experimental steps are: 1) Raw material pretreatment: Red mud is kept in a high-temperature furnace at 625°C for 185 minutes, blast furnace slag is kept in a high-temperature furnace at 370°C for 145 minutes, and then ground through a 200-mesh sieve. Other industrial raw materials are pretreated in 140°C was processed for 135 minutes to finally obtain a raw material with uniform and stable particle size and composition.
[0054] 2) Mixing: According to the ratio of raw materials, weigh each raw material and mix them evenly in a mortar.
[0055] 3) Melting: Heat the uniformly mixed batch materials to 1495°C in a high-temperature...
PUM
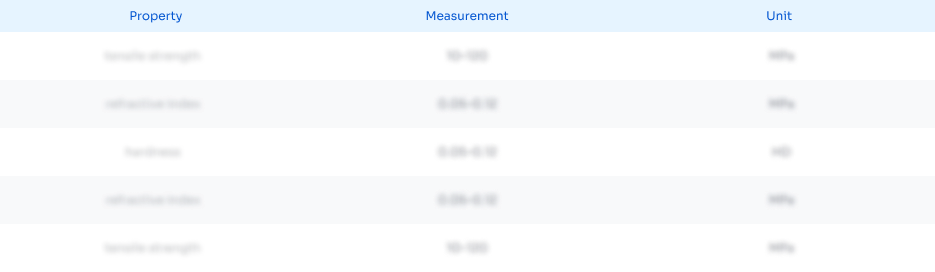
Abstract
Description
Claims
Application Information

- R&D
- Intellectual Property
- Life Sciences
- Materials
- Tech Scout
- Unparalleled Data Quality
- Higher Quality Content
- 60% Fewer Hallucinations
Browse by: Latest US Patents, China's latest patents, Technical Efficacy Thesaurus, Application Domain, Technology Topic, Popular Technical Reports.
© 2025 PatSnap. All rights reserved.Legal|Privacy policy|Modern Slavery Act Transparency Statement|Sitemap|About US| Contact US: help@patsnap.com