Full-automatic grinding and cleaning machine and grinding and cleaning technology thereof
A cleaning machine, fully automatic technology, applied in the direction of grinding machine tools, grinding devices, grinding machine parts, etc., can solve the problems of reduced cleaning effect, transmission failure, slipping, etc.
- Summary
- Abstract
- Description
- Claims
- Application Information
AI Technical Summary
Problems solved by technology
Method used
Image
Examples
Embodiment Construction
[0081] The present invention will be further described below in conjunction with accompanying drawing:
[0082] like Figure 1 to Figure 35 As shown, the technical scheme adopted by the present invention is as follows: a fully automatic grinding and cleaning machine, including a feeding part, a CF cleaning part, a TFT cleaning part, and a two-fluid cleaning and drying part which are sequentially arranged on the machine platform 1 along the flow direction of the glass sheet And the unloading part, the glass sheets to be cleaned are transported to the CF cleaning part through the feeding part in turn, the CF surface is cleaned by the CF cleaning part, the TFR surface is cleaned by the TFT cleaning part, and the CF and TFT surfaces are cleaned by the two-fluid cleaning and drying part Drying is carried out, and the dried glass sheet is exported through the blanking part;
[0083] The above-mentioned feeding part includes a feeding platform 2 and a feeding manipulator 3, the feed...
PUM
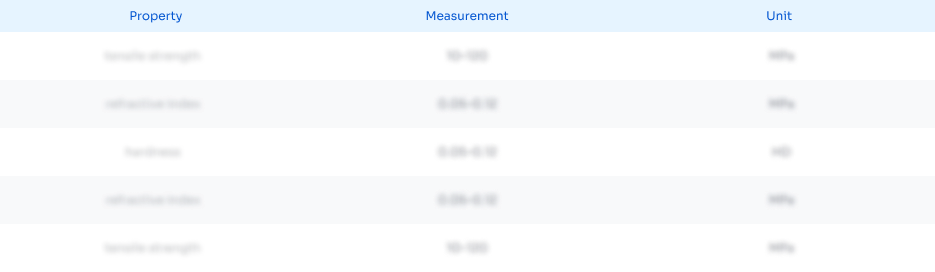
Abstract
Description
Claims
Application Information

- R&D
- Intellectual Property
- Life Sciences
- Materials
- Tech Scout
- Unparalleled Data Quality
- Higher Quality Content
- 60% Fewer Hallucinations
Browse by: Latest US Patents, China's latest patents, Technical Efficacy Thesaurus, Application Domain, Technology Topic, Popular Technical Reports.
© 2025 PatSnap. All rights reserved.Legal|Privacy policy|Modern Slavery Act Transparency Statement|Sitemap|About US| Contact US: help@patsnap.com