Clamping device for taper-cylindrical workpiece
A clamping device and workpiece technology, which are applied in the field of clamping devices for tapered and cylindrical workpieces, can solve the problems of position offset, inconvenient processing of tapered and cylindrical workpieces, large processing errors, etc., and achieve the effect of preventing positional shift.
- Summary
- Abstract
- Description
- Claims
- Application Information
AI Technical Summary
Problems solved by technology
Method used
Image
Examples
Embodiment Construction
[0025] In order to make the object, technical solution and advantages of the present invention clearer, the implementation manner of the present invention will be further described in detail below in conjunction with the accompanying drawings.
[0026] figure 1 It is a structural schematic diagram of a clamping device for a cone-shaped workpiece provided by an embodiment of the present invention. Such as figure 1 As shown, the clamping device includes: a positioning plate 1, a positioning pillar 2, a support ring 3, an expanding block 4, a positioning member and a pressing plate assembly. There is an annular positioning groove 11 on the side of the positioning disc 1 , and the annular side wall with a larger inner diameter is used to fit the outer wall of the flange at one end of the cone-shaped workpiece 7 . The positioning pillar 2 is located on one side of the positioning disk 1 , and the positioning pillar 2 is coaxially arranged with the positioning disk 1 . The suppor...
PUM
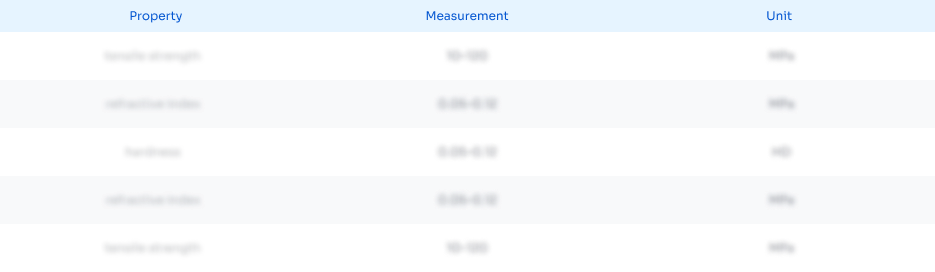
Abstract
Description
Claims
Application Information

- Generate Ideas
- Intellectual Property
- Life Sciences
- Materials
- Tech Scout
- Unparalleled Data Quality
- Higher Quality Content
- 60% Fewer Hallucinations
Browse by: Latest US Patents, China's latest patents, Technical Efficacy Thesaurus, Application Domain, Technology Topic, Popular Technical Reports.
© 2025 PatSnap. All rights reserved.Legal|Privacy policy|Modern Slavery Act Transparency Statement|Sitemap|About US| Contact US: help@patsnap.com