Double bubble column reaction device used for oxidizing p-xylene and reaction process
A reaction device, para-xylene technology, applied in chemical/physical/physical-chemical stationary reactors, preparation of organic compounds, chemical methods for reacting liquid and gaseous media, etc., can solve unfavorable gas and solid-containing slurry It can solve the problems of mixing and flowing of materials, complex structure, etc., so as to improve the comprehensive reaction rate, improve the conversion rate and TA yield, and reduce the investment cost and operating cost.
- Summary
- Abstract
- Description
- Claims
- Application Information
AI Technical Summary
Problems solved by technology
Method used
Image
Examples
Embodiment 1
[0042] In this embodiment, a traditional stirred tank reactor is used to produce terephthalic acid, and the reacted slurry and air continue to react in the first crystallizer. The designed production capacity is 600,000 tons / year, and the annual production time is 8000 Hourly calculation. The specific operating parameters of the reactor and the first crystallizer in this process are given in Table 1, and the operating results of the reactor in this embodiment are shown in Table 2.
[0043] Table 1 Operating parameters of the stirred tank oxidation reactor
[0044]
[0045] Table 2 Operation results of the stirred tank oxidation reactor
[0046]
[0047] Note: 1. The PX conversion rate and TA yield of the first crystallizer refer to the total conversion rate and yield;
[0048] 2. O in exhaust gas 2 , CO 2 and CO concentration refer to the volume fraction of each component in the non-condensable component.
Embodiment 2
[0050] In this example, the double bubble column oxidation reactor proposed by the patent of the present invention is used to produce terephthalic acid, wherein the second reactor is an air-lift internal circulation bubble column reactor with a built-in draft tube. The designed production capacity is 600,000 tons / year, and the annual production time is calculated as 8,000 hours. The specific operating parameters of the two bubble column reactors are given in Table 3, and the structural parameters of the two reactors are given in Table 4.
[0051] Table 3 Operating parameters of double bubble column oxidation reactor
[0052]
[0053]
[0054] Table 4 Structural parameters of double bubble column oxidation reactor
[0055] Structural parameters
high
Guide tube height
unit
m
m
m / m
m
m
m 3
first reactor
5.40
22.00
4.07
-
-
504
...
PUM
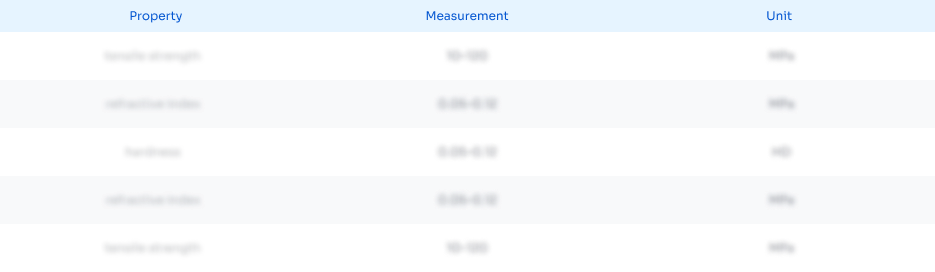
Abstract
Description
Claims
Application Information

- R&D
- Intellectual Property
- Life Sciences
- Materials
- Tech Scout
- Unparalleled Data Quality
- Higher Quality Content
- 60% Fewer Hallucinations
Browse by: Latest US Patents, China's latest patents, Technical Efficacy Thesaurus, Application Domain, Technology Topic, Popular Technical Reports.
© 2025 PatSnap. All rights reserved.Legal|Privacy policy|Modern Slavery Act Transparency Statement|Sitemap|About US| Contact US: help@patsnap.com