High-performance blade processing technology
A processing technology and high-performance technology, which is applied in the field of high-performance blade processing technology, can solve the problems of difficult processing and small volume of turning tool blades, and achieve the effect of increasing block processing speed, improving overall performance, and improving processing efficiency
- Summary
- Abstract
- Description
- Claims
- Application Information
AI Technical Summary
Problems solved by technology
Method used
Examples
Embodiment 1
[0015] A high-performance blade processing technology, including the following steps: a. Using high-speed steel as a raw material, using 3D software to draw a blade model and setting a 1mm margin; b. Using the blade model drawn using 3D software in step a as a processing model, using The stamping die presses the high-speed steel steel to obtain a blade blank; c. Anneal the blank obtained in step b, and place the blank in a vacuum heating furnace at 900°C for 1.5 hours. The blank cools naturally; d. Use a grinder to grind the blade to complete the contour processing without processing the blade; e. Use a high-speed grinder to process the blade, and leave a margin of 0.1mm for blade grinding; f. Use ultrasonic flaw detection for the blank to ensure that there are no cracks inside and on the surface of the blade. If the flaw detection is qualified, proceed to the next step, and discard the unqualified blank; g. Put the flaw-detected blank into a vacuum heating furnace and keep it a...
Embodiment 2
[0018] A high-performance blade processing technology, including the following steps: a. Using high-speed steel as a raw material, using 3D software to draw a blade model and setting a 1mm margin; b. Using the blade model drawn using 3D software in step a as a processing model, using The stamping die presses the high-speed steel steel to obtain a blade blank; c. Anneal the blank obtained in step b, and place the blank in a vacuum heating furnace at a temperature of 960°C for 1.2 hours. The blank cools naturally; d. Use a grinder to grind the blade to complete the contour processing without processing the blade; e. Use a high-speed grinder to process the blade, and leave a margin of 0.15mm for blade grinding; f. The blank uses ultrasonic flaw detection to ensure that there are no cracks inside and on the surface of the blade. If the flaw detection is qualified, proceed to the next step, and the unqualified blank is scrapped; g. Put the flaw-detected blank into a vacuum heating fu...
Embodiment 3
[0021] A high-performance blade processing technology, including the following steps: a. Using high-speed steel as a raw material, using 3D software to draw a blade model and setting a 1mm margin; b. Using the blade model drawn using 3D software in step a as a processing model, using The stamping die presses the high-speed steel steel to obtain a blade blank; c. Anneal the blank obtained in step b, and place the blank in a vacuum heating furnace at a temperature of 1000°C for 1 hour. The blank cools naturally; d. Use a grinder to grind the blade to complete the contour processing without processing the blade; e. Use a high-speed grinder to process the blade, leaving a margin of 0.2mm for blade grinding; f. Use ultrasonic flaw detection for the blank to ensure that there are no cracks inside and on the surface of the blade. If the flaw detection is qualified, proceed to the next step, and discard the unqualified blank; g. Put the flaw-detected blank into a vacuum heating furnace ...
PUM
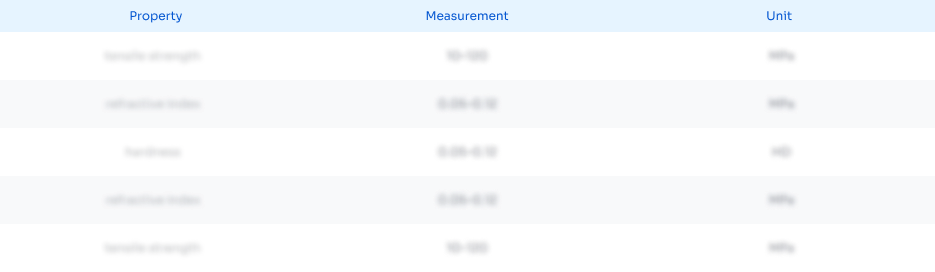
Abstract
Description
Claims
Application Information

- R&D
- Intellectual Property
- Life Sciences
- Materials
- Tech Scout
- Unparalleled Data Quality
- Higher Quality Content
- 60% Fewer Hallucinations
Browse by: Latest US Patents, China's latest patents, Technical Efficacy Thesaurus, Application Domain, Technology Topic, Popular Technical Reports.
© 2025 PatSnap. All rights reserved.Legal|Privacy policy|Modern Slavery Act Transparency Statement|Sitemap|About US| Contact US: help@patsnap.com