Anticorrosion antibacterial defoaming agent and preparation method thereof
A defoamer and anti-corrosion technology, applied in the direction of defoamer, inorganic compound addition, paper, etc., can solve problems such as corrosion of other components of defoamer, discount of defoaming performance, pollution, etc., to improve anti-corrosion performance and promote Enhanced effect
- Summary
- Abstract
- Description
- Claims
- Application Information
AI Technical Summary
Problems solved by technology
Method used
Examples
Embodiment 1
[0021] S1: Add 3 parts of nano-silver oxide, 2 parts of nano-zinc oxide, 2 parts of magnesium 3-picolinate and 1 part of trisilver citrate into 9 parts of 2-methyl propanol. Under ultrasonic dispersion for 3 minutes, the mixture A was obtained;
[0022] S2: Add 7 parts of p-toluenesulfonic acid to the mixed solution A obtained in step S1, then add 6 parts of cross-linked alkanolamine cellulose, 10 parts of terpene resin, 9 parts of 2-methacrolein and 4-methyl- 2 parts of 5-formylthiazole were stirred and reacted at a rate of 500 r / min at a temperature of 80°C for 30 minutes to obtain a mixed solution B;
[0023] S3: Add 7 parts of adenosine cyclic phosphate and 4 parts of azodicarbonamide to 12 parts of phentolamine, and stir and react at a rate of 800 r / min for 30 min at a temperature of 90° C. to obtain a mixed solution C;
[0024] S4: Mix the mixed solution C described in step S3 and the mixed solution B described in step S2, and add 5 parts of N-methyl-3-aminopropyltrimet...
Embodiment 2
[0030] S1: Add 7 parts of nano-silver oxide, 6 parts of nano-zinc oxide, 5 parts of magnesium 3-picolinate and 4 parts of trisilver citrate into 13 parts of 2-methylpropanol, at a temperature of 40°C, at an ultrasonic power of 500W Under ultrasonic dispersion for 8 minutes, the mixture A was obtained;
[0031] S2: Add 11 parts of p-toluenesulfonic acid to the mixed solution A obtained in step S1, then add 10 parts of cross-linked alcoholamine cellulose, 13 parts of terpene resin, 14 parts of 2-methacrolein and 4-methyl- 6 parts of 5-formylthiazole were stirred and reacted at a rate of 500 r / min for 40 min at a temperature of 100°C to obtain a mixed solution B;
[0032] S3: Add 13 parts of adenosine cyclic phosphate and 8 parts of azodicarbonamide to 16 parts of phentolamine, and stir and react at a rate of 800 r / min for 30 minutes at a temperature of 110° C. to obtain a mixed solution C;
[0033] S4: Mix the mixed solution C described in step S3 and the mixed solution B descr...
Embodiment 3
[0039]S1: Add 4 parts of nano-silver oxide, 3 parts of nano-zinc oxide, 3 parts of magnesium 3-picolinate and 1 part of trisilver citrate into 10 parts of 2-methylpropanol, at a temperature of 30°C, at an ultrasonic power of 500W Under ultrasonic dispersion for 3 minutes, the mixture A was obtained;
[0040] S2: Add 8 parts of p-toluenesulfonic acid to the mixed solution A obtained in step S1, then add 7 parts of cross-linked alcoholamine cellulose, 11 parts of terpene resin, 10 parts of 2-methacrolein and 4-methyl- 3 parts of 5-formylthiazole were stirred and reacted at a rate of 500 r / min at a temperature of 80°C for 30 minutes to obtain a mixed solution B;
[0041] S3: 9 parts of adenosine cyclic phosphate and 5 parts of azodicarbonamide were added to 13 parts of phentolamine, and stirred and reacted at a rate of 800 r / min at a temperature of 90° C. for 30 minutes to obtain a mixed solution C;
[0042] S4: Mix the mixed solution C described in step S3 and the mixed solutio...
PUM
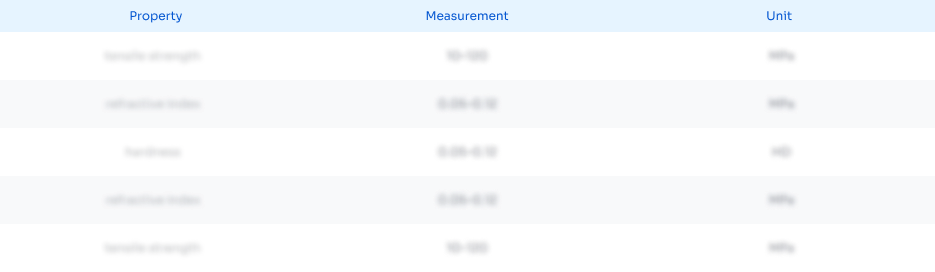
Abstract
Description
Claims
Application Information

- R&D
- Intellectual Property
- Life Sciences
- Materials
- Tech Scout
- Unparalleled Data Quality
- Higher Quality Content
- 60% Fewer Hallucinations
Browse by: Latest US Patents, China's latest patents, Technical Efficacy Thesaurus, Application Domain, Technology Topic, Popular Technical Reports.
© 2025 PatSnap. All rights reserved.Legal|Privacy policy|Modern Slavery Act Transparency Statement|Sitemap|About US| Contact US: help@patsnap.com