A heat insulating filler, its use and preparation method
A technology of thermal insulation filler and ceramic hollow microbeads is applied in the field of thermal insulation filler, which can solve the problems of inability to meet the practical application requirements of industrial production, many raw materials, complicated processes, etc., and achieves elimination of free air layer, simple treatment method, and reduced thermal conductivity. The effect of coefficient resistance
- Summary
- Abstract
- Description
- Claims
- Application Information
AI Technical Summary
Problems solved by technology
Method used
Image
Examples
Embodiment 1
[0021] The opal shale ore is crushed, pulverized, ground and separated to produce opal masterbatches with a diameter of about 100um (ceramic hollow microspheres are generally 10-30um in diameter), and the opal masterbatches are dried at 120°C for 2 hours , the dried opal masterbatch and ceramic hollow microspheres were mixed in a high-speed mixer for 2 hours to make them uniform, and after standing for 30 minutes to cool, the mixture was sieved to separate the ceramic hollow microspheres.
Embodiment 2
[0023] The ceramic hollow microspheres made by Example 1 are added to the following ablation-resistant materials, and the specific proportioning (mass ratio) is as follows:
[0024]
[0025] preparation:
[0026] 1) Weigh 10kg of phenolic resin and add it to a reaction kettle preheated to 65°C and stir for 30 minutes, add 50g of toughening agent and stir for 10min, add 1kg of ceramic hollow microspheres and stir for 10min, add 500g of phenolic hollow microspheres and stir for 10min, and wait in the reaction kettle Finally, stir evenly and take the resin out of the sealed bag and freeze it for later use.
[0027] 2) Fabric: Choose 85tex C-type quartz glass fiber, spiral curly phenolic fiber 20S / 3, aramid fiber-Kevlar K49 and weave according to the quantity ratio (number ratio) of 1:1:1, and weave the yarn Warp and weft density: 9 threads / cm, area density 150g / ㎡.
[0028] The resin in step 1) and the fabric in step 2) are made into a prepreg with a resin content of 40%, and...
PUM
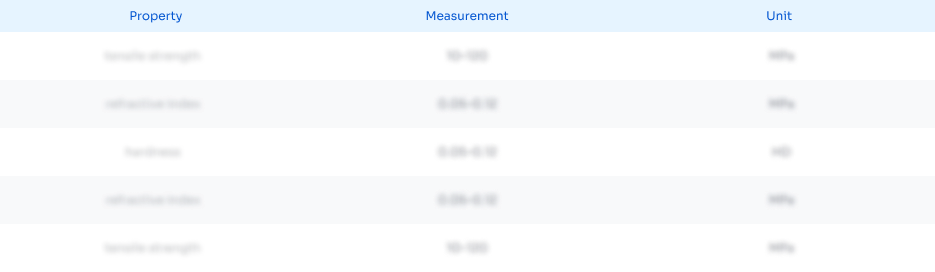
Abstract
Description
Claims
Application Information

- R&D
- Intellectual Property
- Life Sciences
- Materials
- Tech Scout
- Unparalleled Data Quality
- Higher Quality Content
- 60% Fewer Hallucinations
Browse by: Latest US Patents, China's latest patents, Technical Efficacy Thesaurus, Application Domain, Technology Topic, Popular Technical Reports.
© 2025 PatSnap. All rights reserved.Legal|Privacy policy|Modern Slavery Act Transparency Statement|Sitemap|About US| Contact US: help@patsnap.com