Method for improving surface tension and recoatability of organosilicone synthetic leather coating
A silicone synthetic leather and surface tension technology, applied in textiles and papermaking, can solve the problems of poor recoatability, difficult wetting and spreading, poor adhesion between the coating and the substrate, etc., to achieve low energy consumption, improve The effect of surface energy and improved recoatability
- Summary
- Abstract
- Description
- Claims
- Application Information
AI Technical Summary
Problems solved by technology
Method used
Examples
Embodiment 1
[0020] (1) Preparation of double-bond-terminated polyurethane prepolymer: 40 parts of poly(1,3-butylene adipate) diol (PMA2000) with a number average molecular weight of 2000 and polypropylene carbonate with a number average molecular weight of 1000 Dehydrate 15 parts of ester diol (PPC1000), 20 parts of polypropylene glycol (PPG4000) with a number average molecular weight of 4000 (PPG4000) for 3 h at 120 °C under vacuum, and set aside; dehydrated PMA2000, PPC1000, PPG4000, 1.5 parts of 1,4- Add butanediol into the reaction kettle, then add 10 parts of isophorone diisocyanate, 10 parts of hexamethylene diisocyanate, and 0.1 part of organic bismuth catalyst in sequence, raise the temperature to 85 ° C, stir for 1 h, and then add 1 part of internal Cross-linking agent trimethylolpropane, continue to stir and react at 85 °C for 1.5 h, then cool down to 60 °C, add 11 parts of end-capping agent-2-hydroxyethyl acrylate, stir for 8 h, seal and pack for use;
[0021] (2) Preparation o...
Embodiment 2
[0024] (1) Preparation of double bond-terminated polyurethane prepolymer: 20 parts of polypropylene carbonate diol (PPC3000) with a number average molecular weight of 3000 and 30 parts of polypropylene glycol (PPG2000) with a number average molecular weight of 2000 were placed in a vacuum at 120 °C Dehydrate for 4 hours under the same conditions, and set aside; add the dehydrated PPC3000, PPG2000, 1 part of 1,4-butanediol into the reaction kettle, and then add 15 parts of diphenylmethane diisocyanate (MDI-50) and organic bismuth catalyst 0 After stirring and reacting for 1 h, add 0.5 parts of internal crosslinking agent trimethylolpropane, continue stirring and reacting at 75 °C for 1.5 h, then cool down to 60 °C, add end-capping agent 2-hydroxyethyl acrylate 6 parts, stirred and reacted for 7 h, sealed and packaged for use;
[0025] (2) Preparation of modified silicone synthetic leather coating: Add 30 parts of double bond-terminated polyurethane prepolymer and 75 parts of vi...
Embodiment 3
[0028] (1) Preparation of double bond-terminated polyurethane prepolymer: Dehydrate 45 parts of polypropylene glycol (PPG2000) with a number average molecular weight of 2000 under vacuum conditions at 120 °C for 4 h, and set aside; dehydrated PPG2000, 1 part of 1, Add 4-butanediol into the reaction kettle, then add 12 parts of dihexamethylene diisocyanate and 0.05 parts of organic bismuth catalyst in sequence, raise the temperature to 85 °C, stir and react for 1 hour, then add 1 part of internal crosslinking agent trimethylol Propane, continue to stir and react at 85 °C for 1.5 h, then cool down to 60 °C, add 7 parts of end-capping agent 2-hydroxyethyl acrylate, stir for 7 h, seal and pack for use;
[0029] (2) Preparation of modified silicone synthetic leather coating: Add 48 parts of double bond-terminated polyurethane prepolymer and 72 parts of vinyl-terminated silicone oil with a vinyl content of 0.3% to hydrogen-containing silicone oil with a hydrogen content of 0.8%. 30 ...
PUM
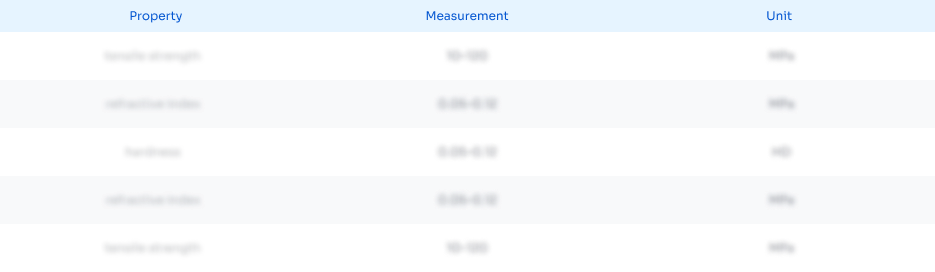
Abstract
Description
Claims
Application Information

- R&D
- Intellectual Property
- Life Sciences
- Materials
- Tech Scout
- Unparalleled Data Quality
- Higher Quality Content
- 60% Fewer Hallucinations
Browse by: Latest US Patents, China's latest patents, Technical Efficacy Thesaurus, Application Domain, Technology Topic, Popular Technical Reports.
© 2025 PatSnap. All rights reserved.Legal|Privacy policy|Modern Slavery Act Transparency Statement|Sitemap|About US| Contact US: help@patsnap.com