A kind of method of heavy oil pretreatment
A pretreatment and heavy oil technology, which is applied in the direction of multi-stage series refining process treatment, can solve the problems of low separation efficiency, increase equipment investment and energy consumption, and achieve the purpose of improving separation speed and efficiency, increasing yield, reducing The effect of small impact
- Summary
- Abstract
- Description
- Claims
- Application Information
AI Technical Summary
Problems solved by technology
Method used
Image
Examples
Embodiment 1
[0028] This example is an implementation of the pretreatment method for the vacuum residue raw material. The vacuum residue raw material enters the visbreaking unit for visbreaking. After moderate visbreaking, a visbroken residue is obtained. Add a composite modifier to the visbreaking residue, which is made of polyacrylamide (CPAM), polyaluminum chloride (PAC), 2,6-di-tert-butyl-4-methylphenol ( BHT) and N,N'-disalicylidene propylenediamine, the weight ratio is 20:40:60:1, and the addition amount of the composite modifier is 0.05% of the weight of the vacuum residue raw material. The mixture enters a continuous settling device for continuous settling, and the operating conditions are as follows: the temperature is 80° C., and the operating pressure is the pressure at which the composite modifier is kept in a liquid phase at the operating temperature. The overflow material is obtained at the overflow outlet of the continuous settling device, and the volume yield of the overf...
Embodiment 2
[0032] Same as Example 1, except adding polyacrylamide (CPAM), polyaluminum chloride (PAC), 2,6-di-tert-butyl-4-methylphenol (BHT) and N, N'-disalicylidene Propylenediamine is mixed in a weight ratio of 30:60:60:1. Wherein, the volume yield of the overflow material obtained is 68%, and the properties of the overflow material are shown in Table 4.
Embodiment 3
[0034] Same as Example 1, except adding polyacrylamide (CPAM), polyaluminum chloride (PAC), 2,6-di-tert-butyl-4-methylphenol (BHT) and N, N'-disalicylidene The weight ratio of propylenediamine mixed is 20:40:80:2. Wherein, the resulting overflow material volume yield is 72%.
PUM
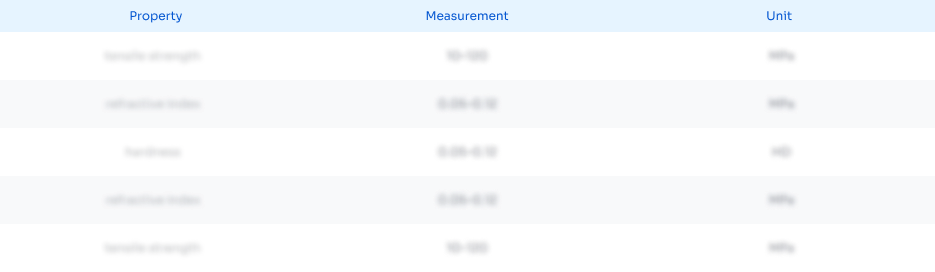
Abstract
Description
Claims
Application Information

- R&D
- Intellectual Property
- Life Sciences
- Materials
- Tech Scout
- Unparalleled Data Quality
- Higher Quality Content
- 60% Fewer Hallucinations
Browse by: Latest US Patents, China's latest patents, Technical Efficacy Thesaurus, Application Domain, Technology Topic, Popular Technical Reports.
© 2025 PatSnap. All rights reserved.Legal|Privacy policy|Modern Slavery Act Transparency Statement|Sitemap|About US| Contact US: help@patsnap.com