Etching paste and preparation method thereof
A technology of etching paste and main features, applied in the field of etching paste and its preparation, can solve the problems of many raw materials and the like
- Summary
- Abstract
- Description
- Claims
- Application Information
AI Technical Summary
Problems solved by technology
Method used
Examples
Embodiment 1
[0032] Etching paste preparation process:
[0033] Raw materials by mass percentage
[0034] Phosphoric acid 20%
[0035] water 3%
[0036] Water-based polyurethane thickener 30%
[0037] Polyether modified silicone leveling agent 0.3%
[0039] Fumed silica 2%
[0040] Glycerol 42.2%
[0041] Carbon black 2%
[0042] Add the selected raw materials into the mixer container with stirring and dispersing cooling water;
[0043] First mix at 60rpm for 3 minutes;
[0044] Turn on the dispersion switch;
[0045] Disperse at 900rpm for 10 minutes;
[0046] Stir for 3 minutes under 120rpm rotating speed again;
[0047] The product is obtained.
[0048] Etching process:
[0049] The etching paste is screen-printed on the glass or PET film coated with ITO film through a 300-mesh screen;
[0050] Put it in an oven and bake at 120°C for 20 minutes.
[0051] Remove the glass or PET film and cool
[0052] Clean the etching paste with water, spr...
Embodiment 2
[0055] Etching paste preparation process:
[0056] Raw materials by mass percentage
[0057] Phosphoric acid 10%
[0058] water 10%
[0059] Associative water-based polyurethane thickener 10%
[0060] Leveling wetting agent 0.3%
[0061] Defoamer 0.5%
[0062] Thixotropic agent 6%
[0063] Glycerol 48.2%
[0064] Carbon black 2%
[0065] Add the selected raw materials into the mixer container with stirring and dispersing cooling water;
[0066] First mix at 60rpm for 3 minutes;
[0067] Turn on the distribution switch;
[0068] Disperse at 800rpm for 10 minutes;
[0069] Stir for 3 minutes under 150rpm rotating speed again;
[0070] The product is obtained.
[0071] Etching process:
[0072] The etching paste is screen-printed on the glass or PET film coated with ITO film through a 300-mesh screen;
[0073] Put it in an oven and bake at 140°C for 30 minutes.
[0074] Remove the glass or PET film and cool
[0075] Clean the etching paste with water, spray or ult...
Embodiment 3
[0078] Etching paste preparation process:
[0079] Raw materials by mass percentage
[0080] Phosphoric acid 1%
[0081] water 3%
[0082] Associative water-based polyurethane thickener 20%
[0083] Leveling wetting agent 0.3%
[0084] Defoamer 0.5%
[0085] Thixotropic agent 9%
[0086] Glycerol 64.2%
[0087] Carbon black 2%
[0088] Add the selected raw materials into the mixer container with stirring and dispersing cooling water;
[0089] First mix at 60rpm for 3 minutes;
[0090] Turn on the distribution switch;
[0091] Disperse at 1000rpm for 10 minutes;
[0092] Stir for 3 minutes under 100rpm rotating speed again;
[0093] The product is obtained.
[0094] Etching process:
[0095] The etching paste is screen-printed on the glass or PET film coated with ITO film through a 300-mesh screen;
[0096] Put it in an oven and bake at 180°C for 20 minutes.
[0097] Remove the glass or PET film and cool
[0098] Clean the etching paste with water, spray or ultras...
PUM
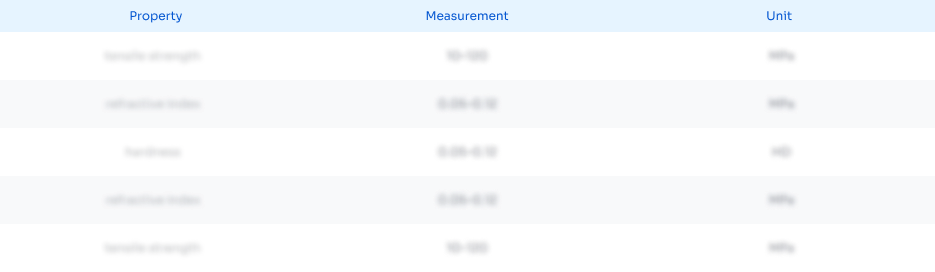
Abstract
Description
Claims
Application Information

- R&D
- Intellectual Property
- Life Sciences
- Materials
- Tech Scout
- Unparalleled Data Quality
- Higher Quality Content
- 60% Fewer Hallucinations
Browse by: Latest US Patents, China's latest patents, Technical Efficacy Thesaurus, Application Domain, Technology Topic, Popular Technical Reports.
© 2025 PatSnap. All rights reserved.Legal|Privacy policy|Modern Slavery Act Transparency Statement|Sitemap|About US| Contact US: help@patsnap.com