Thermal insulation dry-mixed mortar base material and preparation method thereof
A technology of dry-mixed mortar and base material, applied in the field of thermal insulation mortar, can solve the problems of insufficient comprehensive utilization of red mud, insufficiency, etc., and achieve the effects of wide production and application, low production cost and good thermal insulation performance.
- Summary
- Abstract
- Description
- Claims
- Application Information
AI Technical Summary
Problems solved by technology
Method used
Image
Examples
Embodiment 1
[0028] Produce 100 kilograms of powdered anti-cracking additives, then 50 kilograms (5 parts by weight) of epoxidized octadecyl-conjugated triene-9,11,13-acid triglycerides, 20 kilograms (2 parts by weight) of lignocellulose , 20 kilograms (2 parts by weight) of 2-hydroxyethyl methacrylate and 10 kilograms (1 part by weight) of dibutyltin dilaurate are put into the mixer and dry mixed evenly (mixed for about 20 minutes) to form the anti-cracking additive.
[0029] To produce 500 kg of thermal insulation dry-mixed mortar base product of the present invention, 300 kg of red mud and 30 kg of rare earth powder are added with water to form a slurry, and a non-volatile acid solution is added to adjust the pH value of the slurry to 7-8 Dry and grind the powder to obtain powder, and mix the powder with 50 kg of limestone, 30 kg of rare earth powder, 50 kg of redispersible rubber powder, and 40 kg of powdered anti-cracking additive to form a finished product.
Embodiment 2
[0031] Produce 128 kilograms of powdered anti-cracking additives, then respectively 80 kilograms (10 parts by weight) of epoxidized octadecanoconjugated triene-9,11,13-acid triglycerides, 24 kilograms (3 parts by weight) of lignocellulose ), 16 kilograms (2 parts by weight) of 2-hydroxyethyl methacrylate and 8 kilograms (1 part by weight) of dibutyltin dilaurate are put into the mixer and dry-mixed (about 20 minutes) to form a finished product.
[0032] To produce 500 kg of thermal insulation dry-mixed mortar base product of the present invention, 250 kg of red mud and 50 kg of rare earth powder are added with water to form a slurry, and a non-volatile acid solution is added to adjust the pH value of the slurry to 7-8 Dry and grind the powder to obtain powder, and mix the powder with 50 kg of limestone, 50 kg of rare earth powder, 50 kg of redispersible rubber powder, and 50 kg of powdered anti-cracking additive to form a finished product.
Embodiment 3
[0034] The thermal insulation dry-mixed mortar base material product obtained in embodiment 1 and embodiment 2 is made into a thermal insulation board with the same specification and size as the existing sales thermal insulation board, and its thermal insulation performance is tested. The test process is as follows:
[0035] Place three insulation boards evenly on the edge of a circular test board, and place continuous burning fireworks in the middle of the circular test board, and test the inner and outer wall temperatures of the three insulation boards every 10 minutes.
[0036] The final thermal insulation performance test results are shown in Table 1.
[0037] Table 1 Insulation performance test results
[0038]
PUM
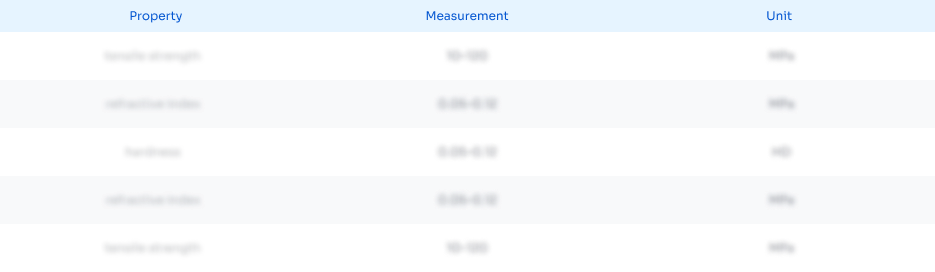
Abstract
Description
Claims
Application Information

- R&D Engineer
- R&D Manager
- IP Professional
- Industry Leading Data Capabilities
- Powerful AI technology
- Patent DNA Extraction
Browse by: Latest US Patents, China's latest patents, Technical Efficacy Thesaurus, Application Domain, Technology Topic, Popular Technical Reports.
© 2024 PatSnap. All rights reserved.Legal|Privacy policy|Modern Slavery Act Transparency Statement|Sitemap|About US| Contact US: help@patsnap.com