Method for preparing hollow magnesium aluminate spinel ceramic fiber by using reed fibers
A technology for hollow magnesia-aluminum spinel and reed fibers, which is applied in the field of preparing hollow magnesia-aluminum spinel ceramic fibers, can solve the problems of high requirement of reaction conditions, unfavorable thermal insulation performance, large energy consumption of solid-phase method, etc. Good appearance, strong alkali corrosion resistance, and the effect of shortening the immersion time
- Summary
- Abstract
- Description
- Claims
- Application Information
AI Technical Summary
Problems solved by technology
Method used
Image
Examples
Embodiment 1
[0040] Get 2.943g of aluminum chloride hexahydrate and dissolve in 20ml of alcohol with a volume fraction of 50%, add 1.238g of magnesium chloride hexahydrate, prepare a concentration of 10% impregnating solution, and now the mol ratio of aluminum to magnesium is 2: 1. Immerse the reed fiber in the above solution, soak for 15 minutes, take it out and dry it; raise the temperature of the dried reed fiber to 1100°C in the air, keep it warm for 1h, and the heating curve is: room temperature ~ 300°C, 2°C / min; 300~ 1100°C, 10°C / min, heat preservation at 1100°C for 60 minutes, and finally cooling with the furnace to prepare hollow magnesium-aluminum spinel fibers. From figure 1 The X-ray diffraction pattern in the figure shows that the material has a molecular formula of Al 2 o 3 · MgO. figure 2 The high magnification image of the scanning electron microscope of the prepared magnesium aluminum spinel fiber shows that the surface of the fiber is relatively smooth, the degree of ...
Embodiment 2
[0042] Take 4.43g of aluminum chloride hexahydrate and dissolve it in 20ml of alcohol with a volume fraction of 50%, add 2.79g of magnesium chloride hexahydrate, and prepare an impregnation solution with a mass fraction of 15%. At this time, the molar ratio of aluminum to magnesium is 133 :100. Immerse the reed fiber in the above solution, soak for 15 minutes, take it out and dry it; raise the temperature of the dried reed fiber to 1100°C in the air, keep it warm for 1h, and the heating curve is: room temperature ~ 300°C, 2°C / min; 300~ 1100°C, 10°C / min, heat preservation at 1100°C for 60 minutes, and finally cooling with the furnace to prepare hollow magnesium-aluminum spinel fibers. Figure 4 Shown is the high magnification image of the prepared magnesium aluminum spinel fiber scanning electron microscope, it can be seen that the hollowness of the fiber is relatively high, and the wall thickness of the fiber is relatively uniform. Figure 5 Shown is a low magnification image...
Embodiment 3
[0044] Get 1.593g of aluminum chloride hexahydrate and dissolve in 20ml of alcohol with a volume fraction of 50%, add 0.224g of magnesium chloride hexahydrate, and prepare a concentration of 5% impregnating solution. At this time, the mol ratio of aluminum element to magnesium element is 600: 100. Immerse the reed fiber in the above solution, soak for 15 minutes, take it out and dry it; raise the temperature of the dried reed fiber to 1100°C in the air, keep it warm for 1h, and the heating curve is: room temperature ~ 300°C, 2°C / min; 300~ 1300°C, 10°C / min, heat preservation at 1300°C for 60 minutes, and finally cooling with the furnace to prepare hollow magnesium-aluminum spinel fibers. Figure 6 Shown is a low magnification image of a magnesium aluminum spinel fiber scanning electron microscope, showing that the fiber length is long and continuous.
PUM
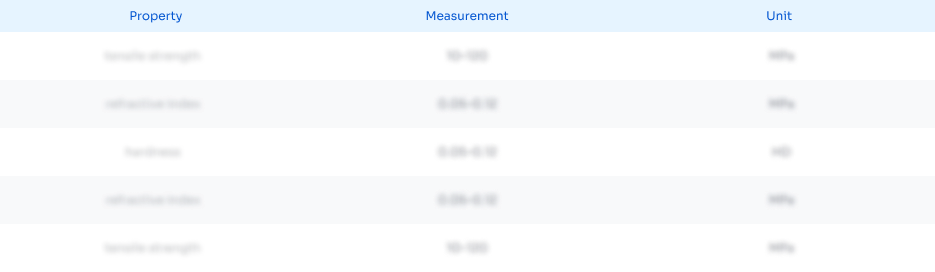
Abstract
Description
Claims
Application Information

- Generate Ideas
- Intellectual Property
- Life Sciences
- Materials
- Tech Scout
- Unparalleled Data Quality
- Higher Quality Content
- 60% Fewer Hallucinations
Browse by: Latest US Patents, China's latest patents, Technical Efficacy Thesaurus, Application Domain, Technology Topic, Popular Technical Reports.
© 2025 PatSnap. All rights reserved.Legal|Privacy policy|Modern Slavery Act Transparency Statement|Sitemap|About US| Contact US: help@patsnap.com