Reforming hydrogen production reactor, conversion furnace, and reforming hydrogen production reaction method
A reforming hydrogen production and reactor technology, applied in chemical instruments and methods, hydrogen, inorganic chemistry, etc., can solve the problems of increasing the energy consumption of the raw gas compressor, increasing the number of catalyst active centers, and the catalyst being prone to carbon deposition and deactivation. , to achieve the effect of total reduction, long service life, and not easy carbon deposition and inactivation
- Summary
- Abstract
- Description
- Claims
- Application Information
AI Technical Summary
Problems solved by technology
Method used
Image
Examples
Embodiment 1
[0091] like figure 1 , figure 2 , image 3 As shown, the reforming hydrogen production reactor adopted in this embodiment includes a pressure-bearing shell 12 comprising a first straight pipe 11 and a second straight pipe 14 at the lower end. 19×1000mm heat exchange tubes 6 constitute a heat exchange area 15 (not all shown in the figure) and a catalytic reaction area 13, the first straight pipe 11 is provided with an air inlet 1, and the lower part of the second straight pipe 14 is provided with an air outlet 2. The catalytic reaction zone is composed of a flat micro-catalytic reaction plate 10, the angle between the flat plate and the horizontal direction is 90°, the micro-catalytic reaction plate 10 is spirally distributed around the central tube, the central tube 6, the catalytic reaction zone 13, the heat exchange zone 15 and the The housing 12 is coaxially arranged; the micro-catalytic reaction plate 10 of the catalytic reaction zone 13 is connected and fixed with th...
Embodiment 2
[0102] like Figure 4 , Figure 5 , image 3 As shown, the reforming hydrogen production reactor and the reforming furnace of the present embodiment are the same as the reactor size of the embodiment 1, the distance between two adjacent catalytic reaction plates, the distance between the annular gaps, the substrate material of the micro-reaction plate and the active component per unit area NiO The payload parameters are the same. The difference from Example 1 is that the micro-catalysis reaction plate 10 of the present embodiment takes the central tube 6 as the center of a circle, and the micro-catalysis reaction plate 10 is radially and evenly arranged around the central tube 6, and the micro-catalysis reaction plate 10 is respectively placed on the top of the catalytic reaction zone. The sealing plate 5 and the sealing plate 8 at the bottom of the catalytic reaction zone are connected and fixed. The reforming hydrogen production reactor and reformer of this embodiment are...
Embodiment 3
[0107] like Image 6 , Figure 7 , image 3 As shown, the reforming hydrogen production reactor and the reforming furnace of the present embodiment are the same as the reactor size of the embodiment 2, the distance between two adjacent catalytic reaction plates, the distance between the ring gaps, the matrix material of the micro-reaction plate and the active component NiO per unit area. The payload parameters are the same. The difference from Example 1 is that the micro-catalytic reaction plate 10 is cylindrical and includes an upper catalytic reaction plate and a lower catalytic reaction plate coaxially arranged alternately at intervals, and the micro-catalytic reaction plate 10 is in the same shape as the housing 12 and the central tube 6. The axis is set, the upper micro catalytic reaction plate is vertically sealed and fixed with the top sealing plate 5 of the catalytic reaction zone, and the lower micro catalytic reaction plate is vertically sealed and fixed with the b...
PUM
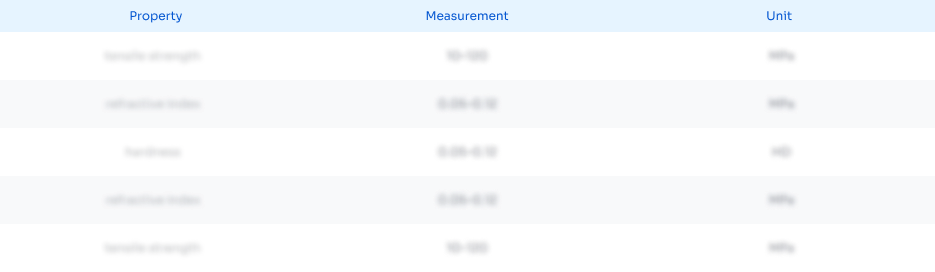
Abstract
Description
Claims
Application Information

- R&D
- Intellectual Property
- Life Sciences
- Materials
- Tech Scout
- Unparalleled Data Quality
- Higher Quality Content
- 60% Fewer Hallucinations
Browse by: Latest US Patents, China's latest patents, Technical Efficacy Thesaurus, Application Domain, Technology Topic, Popular Technical Reports.
© 2025 PatSnap. All rights reserved.Legal|Privacy policy|Modern Slavery Act Transparency Statement|Sitemap|About US| Contact US: help@patsnap.com