Electromagnetic driving galvanometer for reducing rocking motion
A technology of electromagnetic drive and rocking motion, applied in the direction of optical components, optics, instruments, etc., can solve the problems of poor driving effect, achieve the effects of less energy loss, high energy utilization rate, and improved stability
- Summary
- Abstract
- Description
- Claims
- Application Information
AI Technical Summary
Problems solved by technology
Method used
Image
Examples
Embodiment 1
[0048] From Figure 4 It can be seen that the electromagnetically driven oscillating mirror in this embodiment mainly includes an electromagnetic oscillating mirror chip 31, a structure 32 and a driving magnetic circuit 34. Among them, the structure 32 supports and fixes the electromagnetic vibrating mirror chip 31 and the driving magnetic circuit 32, combines the electromagnetic vibrating mirror chip 31 and the driving magnetic circuit 32, and ensures the relative position of the two, and provides the external interface of the electromagnetic vibrating mirror at the same time (including mechanical interfaces or fixed electrical components or interfaces).
[0049] The electromagnetic vibrating mirror chip 31 of this embodiment includes a movable mirror 11, a torsion beam 12 and a fixed frame 13, and the movable mirror 11 is fixed on the fixed frame 13 through the torsion beam 12. The opposite side of the movable mirror 11 is provided with a magnetic material 14 and a reinforcin...
Embodiment 2
[0059] On the basis of Embodiment 1, this embodiment discloses an electromagnetically driven oscillating mirror, from Figure 3a and Figure 3b It can be seen that the electromagnetically driven oscillating mirror in this embodiment includes a movable mirror 11, a torsion beam 12, a fixed frame 13, a reinforcing rib 15 on the opposite side of the mirror, and a magnetic material 14, and the movable mirror 11 is fixed on the fixed frame 13 by the torsion beam 12. . In this embodiment, the center of the reinforcing rib 15 is ring-shaped, and is arranged on the opposite side of the movable mirror 11. The magnetic material 14 passes through the central ring of the reinforcing rib 15 and is pasted on the opposite side of the movable mirror 11, and the reinforcing rib 15 limits the magnetic material 14. . In other embodiments, the reinforcing rib can be in any other shape, and the magnetic material can be pasted on the surface of the reinforcing rib.
[0060] From Figure 3c It ...
Embodiment 3
[0062] Between the electromagnetic oscillating mirror chip 31 and the structure 32, due to different materials and different thermal expansion coefficients, the galvanizing mirror structure will generate stress when the system working environment temperature changes, resulting in changes in the working performance of the galvanizing mirror, such as resonance frequency, etc., from Figure 4 It can be seen that in this embodiment, on the basis of the first embodiment, a stress buffering structure 33 is provided between the electromagnetic vibrating mirror chip 31 and the structure body 32 . The stress buffering structure 33 can be positioned and fixed on the structure 32, and the electromagnetic vibrating mirror chip 31 can be positioned and fixed on the stress buffering structure 33; Thermal stress problem caused by different coefficients of thermal expansion, the stress buffering structure 33 material should be a material close to the thermal expansion coefficient of the electr...
PUM
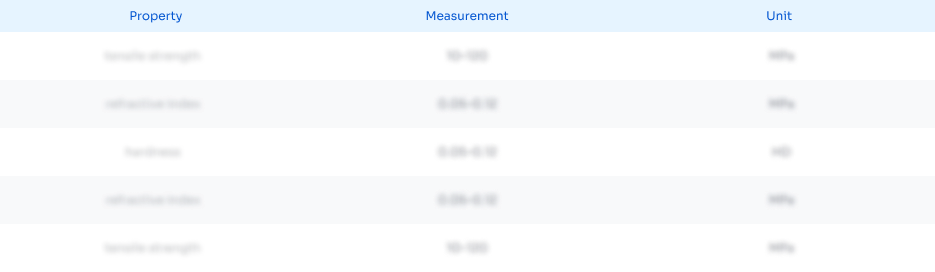
Abstract
Description
Claims
Application Information

- R&D
- Intellectual Property
- Life Sciences
- Materials
- Tech Scout
- Unparalleled Data Quality
- Higher Quality Content
- 60% Fewer Hallucinations
Browse by: Latest US Patents, China's latest patents, Technical Efficacy Thesaurus, Application Domain, Technology Topic, Popular Technical Reports.
© 2025 PatSnap. All rights reserved.Legal|Privacy policy|Modern Slavery Act Transparency Statement|Sitemap|About US| Contact US: help@patsnap.com