Casting process for producing precoated sand shell core rotor with steel shots as filling material
A casting process and filler technology, which is applied in the field of casting process for producing grease-coated sand shell core rotors, can solve the problems of unqualified metallographic structure and mechanical properties of the body, shrinkage holes and shrinkage porosity in the center of castings, and slow cooling rate of molten iron. and other problems, to solve the internal defects of the rotor, improve the metallographic structure, and reduce the production cost.
- Summary
- Abstract
- Description
- Claims
- Application Information
AI Technical Summary
Problems solved by technology
Method used
Image
Examples
Embodiment 1
[0025] refer to figure 1 , a casting process for producing a grease-coated sand shell core rotor with steel shot 4 as a filler, comprising the following steps:
[0026] Step 1: use the coated sand to make the shell core and the built-in core 7, combine the shell cores to form the coated sand shell 2, and put the built-in core 7 into the coated sand shell 2;
[0027] Step 2: Put the coated sand shell 2 into the container 1, and fill the container 1 so that the steel shot 4 wraps the coated sand shell 2, and finally shake the steel shot 4 firmly;
[0028] Step 3: place sprue cup 6 and riser on top of coated sand shell 2;
[0029] Step 4: The molten iron of the ductile cast iron is smoothly poured into the coated sand shell 2 through the sprue cup 6, and cast into shape;
[0030] Step 5: After the molten iron is completely solidified, the cast rotor 3 is obtained.
[0031] The specification of the steel shot 4 in the said step 2 is 3mm. The temperature of molten iron casting ...
Embodiment 2
[0033] refer to figure 1 , a casting process for producing a grease-coated sand shell core rotor with steel shot 4 as a filler, comprising the following steps:
[0034] Step 1: use the coated sand to make the shell core and the built-in core 7, combine the shell cores to form the coated sand shell 2, and put the built-in core 7 into the coated sand shell 2;
[0035] Step 2: Put the coated sand shell 2 into the container 1, and fill the container 1 so that the steel shot 4 wraps the coated sand shell 2, and finally shake the steel shot 4 firmly;
[0036] Step 3: place sprue cup 6 and riser on top of coated sand shell 2;
[0037] Step 4: The molten iron of the ductile cast iron is smoothly poured into the coated sand shell 2 through the sprue cup 6, and cast into shape;
[0038] Step 5: After the molten iron is completely solidified, the cast rotor 3 is obtained.
[0039] In the first step, a core shooting machine is used to make the shell core and the built-in core 7 . In t...
Embodiment 3
[0041] refer to figure 1 , a casting process for producing a grease-coated sand shell core rotor with steel shot 4 as a filler, comprising the following steps:
[0042] Step 1: use the coated sand to make the shell core and the built-in core 7, combine the shell cores to form the coated sand shell 2, and put the built-in core 7 into the coated sand shell 2;
[0043] Step 2: Put the coated sand shell 2 into the container 1, and fill the container 1 so that the steel shot 4 wraps the coated sand shell 2, and finally shake the steel shot 4 firmly;
[0044] Step 3: place sprue cup 6 and riser on top of coated sand shell 2;
[0045] Step 4: The molten iron of the ductile cast iron is smoothly poured into the coated sand shell 2 through the sprue cup 6, and cast into shape;
[0046] Step 5: After the molten iron is completely solidified, the cast rotor 3 is obtained.
[0047] In the first step, a core shooting machine is used to make the shell core and the built-in core 7 . In t...
PUM
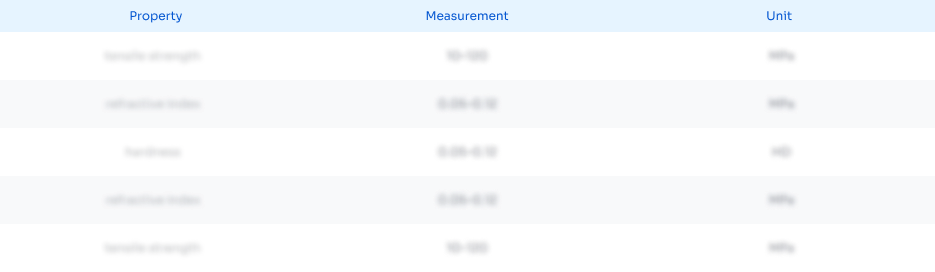
Abstract
Description
Claims
Application Information

- Generate Ideas
- Intellectual Property
- Life Sciences
- Materials
- Tech Scout
- Unparalleled Data Quality
- Higher Quality Content
- 60% Fewer Hallucinations
Browse by: Latest US Patents, China's latest patents, Technical Efficacy Thesaurus, Application Domain, Technology Topic, Popular Technical Reports.
© 2025 PatSnap. All rights reserved.Legal|Privacy policy|Modern Slavery Act Transparency Statement|Sitemap|About US| Contact US: help@patsnap.com