Graphene modified waterborne polyurethane-epoxy resin and preparation method thereof
A water-based polyurethane and graphene modification technology, which is applied in polyurea/polyurethane coatings, coatings, anti-corrosion coatings, etc., can solve the problems of poor hydrolysis resistance and achieve excellent performance, extremely low VOC content, and good electrical conductivity.
- Summary
- Abstract
- Description
- Claims
- Application Information
AI Technical Summary
Problems solved by technology
Method used
Examples
Embodiment 1
[0025] A kind of graphene modified waterborne polyurethane-epoxy resin, its preparation process is as follows:
[0026] a. In a four-port reactor equipped with a thermometer, a condenser, and an agitator, add 3.0 parts of butanediol, 1.5 parts of trimethylolpropane, 6.0 parts of polytetrahydrofuran ether glycol, dihydroxy 2.6 parts of methacrylic acid, heat up to 100℃~110℃ for vacuum dehydration for 1.5~2.0h;
[0027] b. Cool down to 70°C to 75°C, vacuumize, blow in nitrogen to release the pressure, add 1.5 parts of graphene, 8.0 parts of epoxy resin, and dropwise add 14.0 parts of hexamethylene diisocyanate, and the addition is completed in 0.5 to 1 hour. Then add 0.05 parts of dibutyltin dilaurate dropwise, raise the temperature to 80-82°C for 2-2.5 hours, add 6.0 parts of acetone depending on the viscosity of the system, and measure the NCO value until it is consistent with the design value;
[0028] c. Continue to stir to lower the temperature below 35°C, slowly add 1.9 p...
Embodiment 2
[0030] A kind of graphene modified waterborne polyurethane-epoxy resin, its preparation process is as follows:
[0031] a. In a four-port reactor equipped with a thermometer, a condenser, and an agitator, add 2.5 parts of butanediol, 1.5 parts of glycerin, 7.0 parts of polytetrahydrofuran ether glycol, and dimethylol propionic acid in order according to the weight of the formula 2.8 parts, heated to 100℃~110℃ for vacuum dehydration for 1.5~2.0h;
[0032] b. Cool down to 70°C to 75°C, vacuumize, blow in nitrogen to release the pressure, add 1.5 parts of graphene, 4.0 parts of epoxy resin, and dropwise add 16.0 parts of isophorone diisocyanate, and the addition is completed in 0.5 to 1 hour. Then add 0.05 parts of dibutyltin dilaurate dropwise, raise the temperature to 80-82°C for 2-2.5 hours, add 6.0 parts of acetone depending on the viscosity of the system, and measure the NCO value until it is consistent with the design value;
[0033] c. Continue to stir to lower the temper...
Embodiment 3
[0035] A kind of graphene modified waterborne polyurethane-epoxy resin, its preparation process is as follows:
[0036] a. In a four-port reactor equipped with a thermometer, a condenser, and an agitator, add 2.2 parts of neopentyl glycol, 1.2 parts of trimethylolpropane, 6.5 parts of polyether glycol, and two 2.4 parts of hydroxymethylpropionic acid, heated to 100℃~110℃ for vacuum dehydration for 1.5~2.0h;
[0037] b. Cool down to 70°C to 75°C, vacuumize, blow in nitrogen to release the pressure, add 1.6 parts of graphene, 9.0 parts of epoxy resin, and dropwise add 14.0 parts of toluene diisocyanate, and the addition is completed in 0.5 to 1 hour. Then add 0.05 parts of dibutyltin dilaurate dropwise, raise the temperature to 80-82°C for 2-2.5 hours, add 6.5 parts of acetone depending on the viscosity of the system, and measure the NCO value until it is consistent with the design value;
[0038] c. Continue stirring to lower the temperature below 35°C, slowly add 2.0 parts of n...
PUM
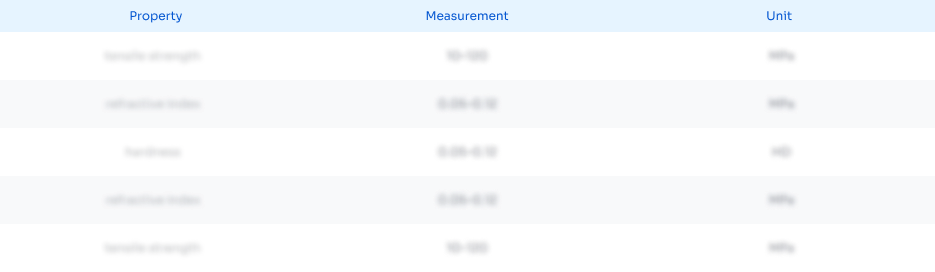
Abstract
Description
Claims
Application Information

- R&D Engineer
- R&D Manager
- IP Professional
- Industry Leading Data Capabilities
- Powerful AI technology
- Patent DNA Extraction
Browse by: Latest US Patents, China's latest patents, Technical Efficacy Thesaurus, Application Domain, Technology Topic, Popular Technical Reports.
© 2024 PatSnap. All rights reserved.Legal|Privacy policy|Modern Slavery Act Transparency Statement|Sitemap|About US| Contact US: help@patsnap.com