Preparation method of ferrum-nickle composite magnetic core subjected to cladding treatment
A coating and magnetic core technology, which is applied in the field of preparation of iron-nickel composite magnetic cores, can solve the problems that the soft magnetic composite materials cannot have excellent magnetic properties, the thermal expansion coefficient of the inorganic insulating layer cannot be changed, and the thermal expansion coefficients differ greatly. Excellent soft magnetic properties, good single-phase property, anti-oxidation effect
- Summary
- Abstract
- Description
- Claims
- Application Information
AI Technical Summary
Problems solved by technology
Method used
Examples
Embodiment 1
[0020] Get ferric chloride, oxalic acid and nickel chloride to be dissolved in hydrochloric acid solution, the mol ratio of standby ferric chloride, oxalic acid and nickel chloride is clarified after ultrasonic dispersion is 3:2:1, and the molar concentration of hydrochloric acid is 1.6 mol / L, The ratio of the total molar amount of ferric chloride, oxalic acid and nickel chloride to hydrochloric acid is 1:3.
[0021] Add complexing agent after the solution is clarified, add acrylamide after the complexing agent is completely dissolved, ultrasonically disperse evenly and clarify, the molar ratio of complexing agent, ferric chloride, nickel chloride and acrylamide is 1:1 : 6; adjust the pH to 2 with ammonia water, and finally heat the mixed solution at 60° C. to cause a thermal polymerization reaction, and the solution turns into a gel.
[0022] Dry the gel in a constant temperature drying oven at 110°C for 7 hours, then place it in a high-temperature furnace at 430°C for 50 min...
Embodiment 2
[0026] Get ferric chloride, oxalic acid and nickel chloride to be dissolved in hydrochloric acid solution, the mol ratio of standby ferric chloride, oxalic acid and nickel chloride is clarified after ultrasonic dispersion is 5:4:2, and the molar concentration of hydrochloric acid is 1.9 mol / L, The ratio of the total molar amount of ferric chloride, oxalic acid and nickel chloride to hydrochloric acid is 3:10.
[0027] Add a complexing agent after the solution is clarified, add acrylamide after the complexing agent is completely dissolved, ultrasonically disperse evenly and clarify, the molar ratio of complexing agent, ferric chloride, nickel chloride and acrylamide is 2:1 : 8; adjust the pH to 3 with ammonia water, and finally heat the mixed solution at 80° C. to cause thermal polymerization to occur, and the solution turns into a gel.
[0028] Dry the gel in a constant temperature drying oven at 120°C for 9 hours, then place it in a high-temperature furnace at 460°C for 70 mi...
PUM
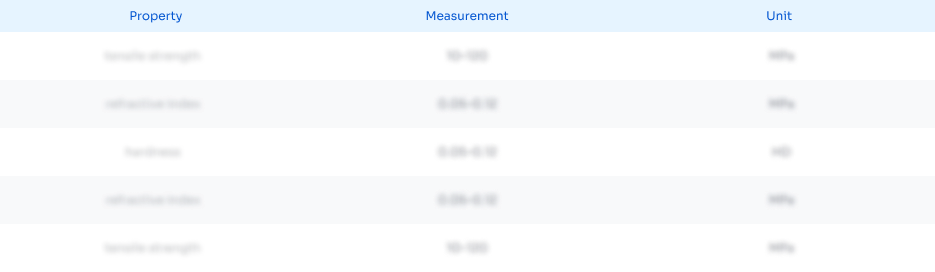
Abstract
Description
Claims
Application Information

- Generate Ideas
- Intellectual Property
- Life Sciences
- Materials
- Tech Scout
- Unparalleled Data Quality
- Higher Quality Content
- 60% Fewer Hallucinations
Browse by: Latest US Patents, China's latest patents, Technical Efficacy Thesaurus, Application Domain, Technology Topic, Popular Technical Reports.
© 2025 PatSnap. All rights reserved.Legal|Privacy policy|Modern Slavery Act Transparency Statement|Sitemap|About US| Contact US: help@patsnap.com