Square copper wire motor stator structure
A technology of motor stator and copper wire, applied in the shape/style/structure of winding insulation, the shape/style/structure of winding conductor, electric components, etc. It can improve the redundancy and reliability, increase the occupancy rate of bare copper and the power density of the motor.
- Summary
- Abstract
- Description
- Claims
- Application Information
AI Technical Summary
Problems solved by technology
Method used
Image
Examples
specific Embodiment approach
[0024] The motor stator of the present invention includes a stator core and a stator winding. The stator winding is arranged on the stator core. The stator winding presents a four-layer structure on the stator core. The stator winding consists of a square cross section. Composed of square copper wires, the stator winding is composed of the first layer of conductors, the second layer of conductors, the third layer of conductors, and the fourth layer of conductors from the outer circle of the stator to the inner circle of the stator. The stator winding has two sets of winding structures. The first layer and the second layer of conductors form a first set of windings, the third layer of conductors and the fourth layer of conductors form a second set of windings, figure 1 with figure 2 They are respectively the arrangement diagrams of the first set of windings and the second set of windings in the stator structure of the square copper wire motor of the present invention, the firs...
PUM
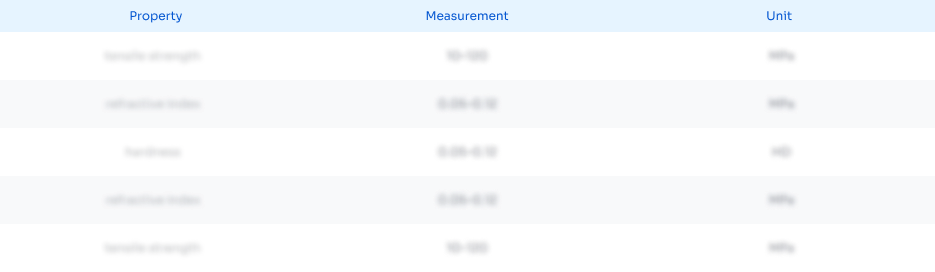
Abstract
Description
Claims
Application Information

- R&D Engineer
- R&D Manager
- IP Professional
- Industry Leading Data Capabilities
- Powerful AI technology
- Patent DNA Extraction
Browse by: Latest US Patents, China's latest patents, Technical Efficacy Thesaurus, Application Domain, Technology Topic, Popular Technical Reports.
© 2024 PatSnap. All rights reserved.Legal|Privacy policy|Modern Slavery Act Transparency Statement|Sitemap|About US| Contact US: help@patsnap.com