Preparation method of wear-resistant and corrosion-resistant UV-curing composite coating for metal members
A composite coating, anti-corrosion technology, used in coatings, anti-corrosion coatings, etc., can solve problems such as poor effect, wear resistance, and poor corrosion resistance, and achieve good system stability, strong acid and alkali resistance, and increased resistance to The effect of corrosion and wear resistance
- Summary
- Abstract
- Description
- Claims
- Application Information
AI Technical Summary
Problems solved by technology
Method used
Image
Examples
Embodiment 1
[0022] A method for preparing a wear-resistant and anti-corrosion UV curing composite coating for metal parts, comprising the following steps
[0023] 1) Resin monomer synthesis: dimerized fatty acid (DA), glycidyl methacrylate (GMA), hydroquinone and benzyltriethylammonium chloride in a molar ratio of 200:200:5:2 Stir at a constant temperature of 120°C and 120r / min for 2 hours in a container with a condensing reflux device. After cooling to room temperature, mix the above synthesized liquid with isocyanatopropyltriethoxysilane (IPTS) in a molar ratio of 1:2 under nitrogen protection Stir at a constant temperature of 70°C and 120r / min in a container for 4 hours, and then obtain the resin monomer after cooling to room temperature;
[0024] 2) Weigh each raw material according to the following parts by weight: 100 parts of resin monomer, 0.5 part of thermal curing accelerator, 5 parts of photoinitiator, 15 parts of modified metal powder, 15 parts of graphite powder, 20 parts of ...
Embodiment 2
[0034] A method for preparing a wear-resistant and anti-corrosion UV-cured composite coating for metal parts, comprising the following steps:
[0035] 1) Resin monomer synthesis: dimerized fatty acid (DA), glycidyl methacrylate (GMA), hydroquinone and benzyltriethylammonium chloride in a molar ratio of 200:200:5:2 Stir at a constant temperature of 120°C and 120r / min for 2 hours in a container with a condensing reflux device. After cooling to room temperature, mix the above synthesized liquid with isocyanatopropyltriethoxysilane (IPTS) in a molar ratio of 1:2 under nitrogen protection Stir at a constant temperature of 70°C and 120r / min in a container for 4 hours, and then obtain the resin monomer after cooling to room temperature;
[0036] 2) Weigh each raw material according to the following parts by weight: 100 parts of resin monomer, 0.5 part of thermosetting accelerator, 3 parts of photoinitiator, 15 parts of modified metal powder, 10 parts of graphite powder, 15 parts of n...
Embodiment 3
[0046] A method for preparing a wear-resistant and anti-corrosion UV curing composite coating for metal parts, comprising the following steps:
[0047]1) Resin monomer synthesis: dimerized fatty acid (DA), glycidyl methacrylate (GMA), hydroquinone and benzyltriethylammonium chloride in a molar ratio of 200:200:5:2 Stir at a constant temperature of 120°C and 120r / min for 2 hours in a container with a condensing reflux device. After cooling to room temperature, mix the above synthesized liquid with isocyanatopropyltriethoxysilane (IPTS) in a molar ratio of 1:2 under nitrogen protection Stir at a constant temperature of 70°C and 120r / min in a container for 4 hours, and then obtain the resin monomer after cooling to room temperature;
[0048] 2) Weigh each raw material according to the following parts by weight: 80 parts of resin monomer, 0.2 part of thermal curing accelerator, 3 parts of photoinitiator, 12 parts of modified metal powder, 12 parts of graphite powder, 20 parts of n...
PUM
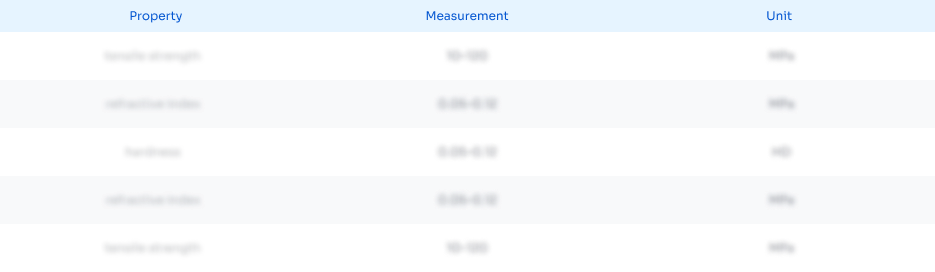
Abstract
Description
Claims
Application Information

- R&D
- Intellectual Property
- Life Sciences
- Materials
- Tech Scout
- Unparalleled Data Quality
- Higher Quality Content
- 60% Fewer Hallucinations
Browse by: Latest US Patents, China's latest patents, Technical Efficacy Thesaurus, Application Domain, Technology Topic, Popular Technical Reports.
© 2025 PatSnap. All rights reserved.Legal|Privacy policy|Modern Slavery Act Transparency Statement|Sitemap|About US| Contact US: help@patsnap.com