Control method for rough pitted surface on surface of 9Ni steel of single-rack steekle mill
A surface roughness, furnace coil mill technology, applied in the field of metallurgy, can solve the problems of single-stand furnace coil mill 9Ni steel surface roughness, pitting, etc., to reduce batch grinding and scrap change judgment, plate surface uniformity, and achieve stable control Effect
- Summary
- Abstract
- Description
- Claims
- Application Information
AI Technical Summary
Problems solved by technology
Method used
Image
Examples
Embodiment Construction
[0021] This embodiment selects billet size specifications 150*2290*8861mm and 150*2290*8843mm (billet thickness*width*length) to roll finished product thickness 46mm and 8mm X7Ni9 steel respectively, and the whole rolling process is as follows figure 1 As shown, the stable control of the surface quality of the 9Ni steel plate in the single-stand steckel mill is realized by optimizing the control of the heating temperature of the heating furnace, the time in the furnace, the descaling of the descaling box, the rolling schedule of the rolling mill and the descaling pass process. The specific optimization is as follows:
[0022] (1) Furnace heating
[0023] Reduce the heating temperature of the heating furnace and control the time of the billet in the furnace. 9Ni steel billets with a thickness of 150mm are intensively scheduled to ensure the same heating system. The distance between billets in the furnace is increased from 150mm to 200mm, and a space is reserved in front of the...
PUM
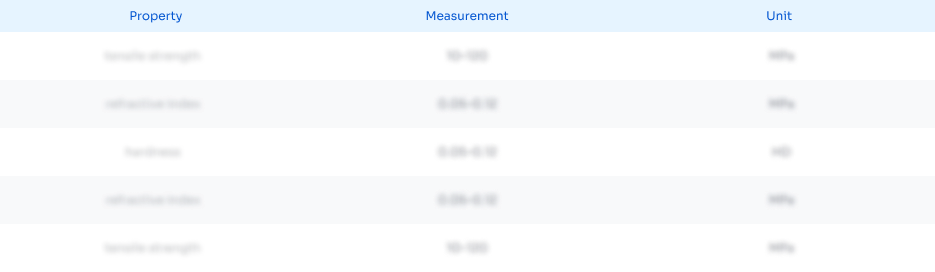
Abstract
Description
Claims
Application Information

- R&D Engineer
- R&D Manager
- IP Professional
- Industry Leading Data Capabilities
- Powerful AI technology
- Patent DNA Extraction
Browse by: Latest US Patents, China's latest patents, Technical Efficacy Thesaurus, Application Domain, Technology Topic, Popular Technical Reports.
© 2024 PatSnap. All rights reserved.Legal|Privacy policy|Modern Slavery Act Transparency Statement|Sitemap|About US| Contact US: help@patsnap.com