Processing method for inner-ring-free cylindrical roller bearing alloy steel solid retainer
A technology of cylindrical roller bearings and solid cages, applied in the field of bearings, can solve problems such as substandard roughness of machining precision pockets, cracks on rolling surfaces, etc., to avoid breakage of broaches, stabilize machining dimensions, and improve geometric accuracy and the effect of dimensional accuracy
- Summary
- Abstract
- Description
- Claims
- Application Information
AI Technical Summary
Problems solved by technology
Method used
Image
Examples
specific Embodiment approach 1
[0019] Specific implementation mode one: combine Figure 1-Figure 6 To illustrate this embodiment, a method for processing an alloy steel solid cage of a cylindrical roller bearing without an inner ring in this embodiment includes the following steps:
[0020] Turning, quenching and tempering, rough grinding of outer diameter, fine turning of both ends, fine turning of inner diameter, uniform grinding of both ends, final grinding of outer diameter, final grinding of inner diameter, turning of inner steps, marking, drilling, milling of square holes, square drawing Hole, deburring, cleaning, stress relief annealing, finishing, roll lock, dynamic balancing, magnetic particle inspection, silver plating, final inspection and packaging processes.
[0021] The following takes the implementation of a certain type of bearing cage made of 40CrNiMoA as an example:
[0022] Step 1: Car forming: turning the inner diameter d to The height dimension S is turned to 23.6-23.7mm, and the out...
specific Embodiment approach 2
[0047] Specific Embodiment 2: The preheating temperature of stress relief annealing in the process of this embodiment is 150±5°C, the preheating time of stress relief annealing is 120±10min, and the final heating temperature of stress relief annealing is 550±5°C.
[0048] Other compositions and connections are the same as in the first embodiment.
specific Embodiment approach 3
[0049] Specific implementation mode three: combination figure 1 To illustrate this embodiment, the process of this embodiment leaves a machining allowance of 0.15-0.25 mm for milling a square hole.
[0050] This setting ensures the accuracy of the subsequent square hole. If the margin is too large, the pocket hole accuracy and surface roughness cannot be guaranteed. If the margin is too small, the milling tool marks during the square hole milling process cannot be completely removed. , can not meet the process requirements.
[0051] Other compositions and connections are the same as those in the second embodiment.
PUM
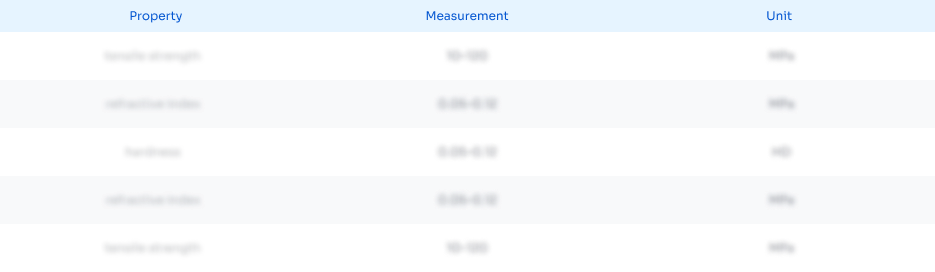
Abstract
Description
Claims
Application Information

- R&D Engineer
- R&D Manager
- IP Professional
- Industry Leading Data Capabilities
- Powerful AI technology
- Patent DNA Extraction
Browse by: Latest US Patents, China's latest patents, Technical Efficacy Thesaurus, Application Domain, Technology Topic, Popular Technical Reports.
© 2024 PatSnap. All rights reserved.Legal|Privacy policy|Modern Slavery Act Transparency Statement|Sitemap|About US| Contact US: help@patsnap.com