Precise casting technology for green sand vacuum sealing model
A technology of vacuum-sealed molding and precision casting, which is applied in the direction of manufacturing tools, casting molding equipment, casting molds, etc. It can solve problems such as dust pollution, long-term vacuuming, and coatings affecting production efficiency, so as to save costs, improve production efficiency, Effect of reducing energy consumption
- Summary
- Abstract
- Description
- Claims
- Application Information
AI Technical Summary
Problems solved by technology
Method used
Image
Examples
Embodiment 1
[0040]In this embodiment, the green sand made of standard casting silica sand, coal powder for casting, bentonite for casting and a small amount of water is used as the molding material. The EVA film is heated by the device; the EVA film that has been heated to form a mirror surface is attached to the mold, and the film is completely adsorbed on the surface of the mold under the action of vacuum negative pressure; Shaking, into a sand mold. After the molding is completed, the upper part of the sand mold is covered with a plastic film, and the vacuum pumping sand box is connected to the vacuum pumping system to pump negative pressure; at the same time, the vacuum valve in the pumping chamber of the negative pressure box is closed; the mold is lifted again to complete a mold-making work; change the model or Use the same process steps as the sand box to complete the upper mold; fasten the upper and lower molds to form the cavity to complete the entire molding work; put the sprue ...
Embodiment 2
[0042] This embodiment produces single-hole large-plane castings, and its technological process is as follows figure 1
[0043] ① Make foam modules, such as figure 2 The foam module shown in the cavity is made of polystyrene foam on the lower surface of the cavity, which is generally formed by foam molding or cutting bonding or cutting processing.
[0044] ②Select the molding material, which is made of standard casting silica sand, coal powder for casting, bentonite for casting and a small amount of water.
[0045] ③Make a vacuum-tight mold, such as Figure 4 As shown, a 0.1mm thick EVA film is selected and heated to 80-120°C to form a mirror surface. Under the action of vacuum negative pressure, the film is pasted on the surface of the model. The negative pressure box of the mold bottom plate is vacuumed at 0.03-0.05Mpa. Then move the model to the vibrating table, and add molding materials while compacting it. At the same time, put the foam module into the mold cavity. A...
Embodiment 3
[0049] This embodiment produces single-hole large-plane castings
[0050] ① Make foam modules, such as figure 2 The foam module shown in the cavity is made of polystyrene foam on the lower surface of the cavity, which is generally formed by foam molding or cutting bonding or cutting processing.
[0051] ② Select the molding material, which is made of standard casting silica sand, casting clay and a small amount of water.
[0052] ③Make a vacuum-tight mold, such as Figure 5 As shown, a 0.1mm thick EVA film is selected and heated to 80-120°C to form a mirror surface. Under the action of vacuum negative pressure, the film is pasted on the surface of the model. The negative pressure box of the mold bottom plate is vacuumed at 0.03-0.05Mpa. Then move the model to the vibrating table, and add molding materials while compacting it. At the same time, put the foam module into the mold cavity. After adding the molding sand, the shaking table stops vibrating, and covers the film on ...
PUM
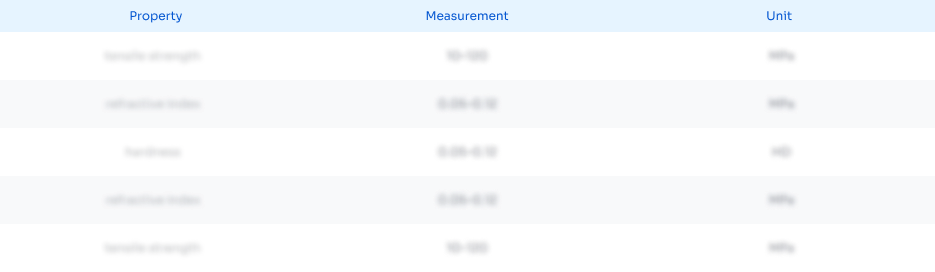
Abstract
Description
Claims
Application Information

- Generate Ideas
- Intellectual Property
- Life Sciences
- Materials
- Tech Scout
- Unparalleled Data Quality
- Higher Quality Content
- 60% Fewer Hallucinations
Browse by: Latest US Patents, China's latest patents, Technical Efficacy Thesaurus, Application Domain, Technology Topic, Popular Technical Reports.
© 2025 PatSnap. All rights reserved.Legal|Privacy policy|Modern Slavery Act Transparency Statement|Sitemap|About US| Contact US: help@patsnap.com