Water-based ink for film printing and preparation method of ink
A water-based ink and film printing technology, applied in the field of printing materials, can solve the problems of water-based ink adhesion fastness, low tinting strength, etc.
- Summary
- Abstract
- Description
- Claims
- Application Information
AI Technical Summary
Problems solved by technology
Method used
Examples
preparation example Construction
[0031]The preparation method of the described water-based ink for film printing, comprises the following steps:
[0032] S1: Add deionized water to the dispersion tank, add calcium carbonate and kaolin under stirring conditions, add the specified amount of pigment after stirring evenly, and prepare the pigment into an aqueous dispersion with a concentration of 40%-60%;
[0033] S2: Add water-based polyurethane-acrylic resin emulsion, defoamer, sodium alkyl sulfate, polyacrylamide, and monoalkoxy titanate to the water dispersion, stir evenly, and then use a high-speed disperser at 5000-6000r / min After dispersing for 60-80 minutes, add it to a sand mill and grind until the particle size is <10μm, and then leave the water-based ink for 30-35 days to obtain the finished product.
Embodiment 1
[0035] The water-based ink for film printing, in parts by weight, includes the following components: 50 parts of water-based polyurethane-acrylic resin emulsion, 55 parts of deionized water, 5 parts of iron oxide red, 5 parts of organic yellow, 2.5 parts of ammonia water 3 parts, 3 parts of calcium carbonate, 3 parts of kaolin, 1.6 parts of polyoxyethylene polyoxypropanol amine ether, 2.5 parts of sodium alkyl sulfate, 1.8 parts of polyacrylamide, 0.3 part of monoalkoxy titanate;
[0036] The water-based polyurethane-acrylic resin emulsion uses butyl acrylate, methyl methacrylate, and methacrylic acid as monomers, and adopts emulsion polymerization to prepare a water-based acrylic resin emulsion, and then it is modified by water-based polyurethane to make water-based polyurethane-acrylic acid. Acrylic resin emulsion; the water-based polyurethane is made of toluene diisocyanate under the effect of dibutyltin dilaurate and polypropylene glycol, methacrylic acid, 1,6-hexanediol, h...
Embodiment 2
[0041] The described water-based ink for film printing comprises the following components in parts by weight: 55 parts of water-based polyurethane-acrylic resin emulsion, 60 parts of deionized water, 4 parts of organic yellow, 4 parts of titanium dioxide, 4 parts of carbon black 2.3 parts of ammonia water, 1 part of calcium carbonate, 4 parts of kaolin, 1.2 parts of polyoxypropylene glyceryl ether, 3.8 parts of sodium alkyl sulfate, 3.5 parts of polyacrylamide, and 0.35 parts of monoalkoxy titanate;
[0042] The water-based polyurethane-acrylic resin emulsion uses butyl acrylate, methyl methacrylate, and methacrylic acid as monomers, and adopts emulsion polymerization to prepare a water-based acrylic resin emulsion, and then it is modified by water-based polyurethane to make water-based polyurethane-acrylic acid. Acrylic resin emulsion; the water-based polyurethane is made of toluene diisocyanate under the effect of dibutyltin dilaurate and polypropylene glycol, methacrylic aci...
PUM
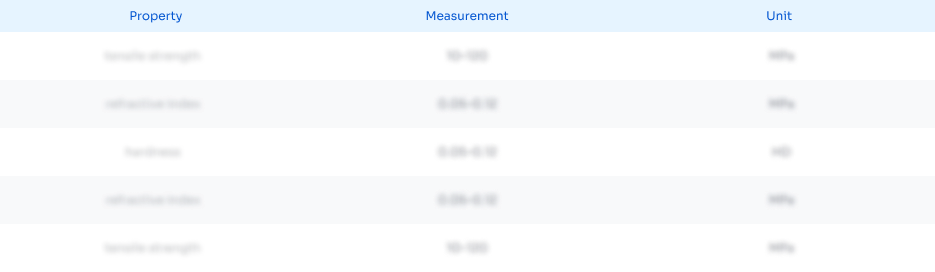
Abstract
Description
Claims
Application Information

- R&D
- Intellectual Property
- Life Sciences
- Materials
- Tech Scout
- Unparalleled Data Quality
- Higher Quality Content
- 60% Fewer Hallucinations
Browse by: Latest US Patents, China's latest patents, Technical Efficacy Thesaurus, Application Domain, Technology Topic, Popular Technical Reports.
© 2025 PatSnap. All rights reserved.Legal|Privacy policy|Modern Slavery Act Transparency Statement|Sitemap|About US| Contact US: help@patsnap.com