An integrated process for coke oven flue gas dry desulfurization, denitrification and purification
A dry desulfurization and flue gas technology, applied in the field of coal chemical industry, can solve the problems of low desulfurization and denitrification efficiency, not too strong practicability, large heat loss, etc., and achieve the effects of less processing costs, prolonging life, and reducing operating costs
- Summary
- Abstract
- Description
- Claims
- Application Information
AI Technical Summary
Problems solved by technology
Method used
Image
Examples
Embodiment 1
[0030] The coke oven flue gas desulfurization and denitrification integrated purification process in a coking plant in Shanxi is shown in the attached figure 1 As shown, the SOx content in the feed gas is 198mg / m 3 , NOx is 1200mg / m 3 , chlorine content 3.5mg / m 3 , fluorine content 0.3mg / m 3 , gas volume is 20000m 3 / h, the temperature is 260°C, the coke oven flue gas first enters the dechlorination reactor 1, and the dechlorination agent is installed 20m 3 , airspeed is 10000h -1 ,, the chlorine and fluorine in the raw material gas react with the active components of the dechlorination agent, are adsorbed on the dechlorination agent, and most of the chlorine and fluorine are removed. After dechlorination, the chlorine and fluorine content in the raw material is less than 0.1mg / m3. Because the dechlorination agent has a large specific surface area, it can absorb a large amount of smoke and dust at the same time, and the smoke and dust in the raw material can be reduced b...
Embodiment 2
[0036] The coke oven flue gas desulfurization and denitrification integrated purification process in a coking plant in Shanxi is shown in the attached figure 1 As shown, the SOx content in the feed gas is 198mg / m 3 , NOx is 1200mg / m 3 , chlorine content 3.5mg / m 3 , fluorine content 0.3mg / m 3 , gas volume is 20000m 3 / h, the temperature is 300°C, the coke oven flue gas first enters the dechlorination reactor 1, and the dechlorination agent is installed 10m 3 , the airspeed is 20000h -1 ,, the chlorine and fluorine in the raw material gas react with the active components of the dechlorination agent, are adsorbed on the dechlorination agent, and most of the chlorine and fluorine are removed. After dechlorination, the chlorine and fluorine content in the raw material is less than 0.1mg / m 3 . Because the dechlorination agent has a large specific surface area, it can absorb a large amount of smoke and dust at the same time, and the smoke and dust in the raw material can be re...
Embodiment 3
[0042] The coke oven flue gas desulfurization and denitrification integrated purification process in a coking plant in Shanxi is shown in the attached figure 1 As shown, the SOx content in the feed gas is 198mg / m 3 , NOx is 1200mg / m 3 , chlorine content 3.5mg / m 3 , fluorine content 0.3mg / m 3 , gas volume is 20000m 3 / h, the temperature is 280°C, the coke oven flue gas first enters the dechlorination reactor 1, and the dechlorination agent 13.3m 3 , airspeed is 1500h -1 ,, the chlorine and fluorine in the raw material gas react with the active components of the dechlorination agent, are adsorbed on the dechlorination agent, and most of the chlorine and fluorine are removed. After dechlorination, the chlorine and fluorine content in the raw material is less than 0.1mg / m 3 . Because the dechlorination agent has a large specific surface area, it can absorb a large amount of smoke and dust at the same time, and the smoke and dust in the raw material can be reduced by 50% aft...
PUM
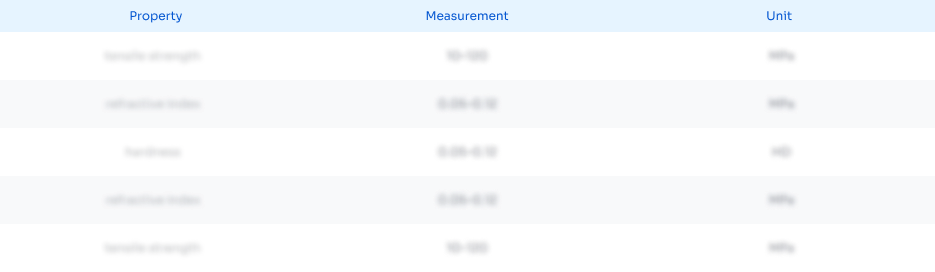
Abstract
Description
Claims
Application Information

- R&D
- Intellectual Property
- Life Sciences
- Materials
- Tech Scout
- Unparalleled Data Quality
- Higher Quality Content
- 60% Fewer Hallucinations
Browse by: Latest US Patents, China's latest patents, Technical Efficacy Thesaurus, Application Domain, Technology Topic, Popular Technical Reports.
© 2025 PatSnap. All rights reserved.Legal|Privacy policy|Modern Slavery Act Transparency Statement|Sitemap|About US| Contact US: help@patsnap.com