Method for synthesizing dinitrotoluene through micro-channel reactor
A micro-channel reactor, dinitrotoluene technology, applied in the chemical industry, can solve the problems of aggravating the rising temperature, equipment corrosion, and high temperature, and achieve the effects of short residence time, safe and reliable production, and low material inventory.
- Summary
- Abstract
- Description
- Claims
- Application Information
AI Technical Summary
Problems solved by technology
Method used
Image
Examples
Embodiment 1
[0022] This embodiment provides a method for synthesizing dinitrotoluene in a microchannel reactor, such as figure 1 As shown, the specific steps are as follows:
[0023] (1) The measured mixed acid, NO 2 The mixed acid is a mixture of concentrated nitric acid and concentrated sulfuric acid, the mass ratio of the two is 1:5, the mass concentration of concentrated nitric acid is 85%, the mass concentration of concentrated sulfuric acid is 98%, and the mixed acid is a mixture of concentrated nitric acid and concentrated sulfuric acid. The molar ratio of concentrated nitric acid is 1:2, toluene and NO 2 The molar ratio is 1:1.08, the reaction temperature is 52°C, and the reaction time is 90s; the reaction equation is as follows:
[0024]
[0025] (2) After the reaction, the gas-liquid separation is carried out first, and the nitrogen oxides in the gas phase are further oxidized and then returned to the system to participate in the reaction again; the liquid phase is allowed to stand f...
Embodiment 2
[0030] This embodiment provides a method for synthesizing dinitrotoluene in a microchannel reactor, such as figure 1 As shown, the specific steps are as follows:
[0031] (1) The measured mixed acid, NO 2 The mixed acid is a mixture of concentrated nitric acid and concentrated sulfuric acid, the mass ratio of the two is 1:7, the concentration of concentrated nitric acid is 88%, the concentration of concentrated sulfuric acid is 95%, and the molar ratio of toluene to concentrated nitric acid 1:3, toluene and NO 2 The molar ratio is 1:1.1, the reaction temperature is 55°C, and the reaction time is 70s; the reaction equation is as follows:
[0032]
[0033] (2) After the reaction, the gas-liquid separation is carried out first, and the nitrogen oxides in the gas phase are further oxidized and then returned to the system to participate in the reaction again; the liquid phase is allowed to stand for stratification, the organic phase is crude mononitrotoluene, and the water phase is mixe...
Embodiment 3
[0038] This embodiment provides a method for synthesizing dinitrotoluene in a microchannel reactor, such as figure 1 As shown, the specific steps are as follows:
[0039] (1) The measured mixed acid, NO 2 The mixed acid is a mixture of concentrated nitric acid and concentrated sulfuric acid, the mass ratio of the two is 1:8, the concentration of concentrated nitric acid is 75%, the concentration of concentrated sulfuric acid is 92%, and the molar ratio of toluene to concentrated nitric acid is 1:5, toluene and NO 2 The molar ratio is 1:1.1, the reaction temperature is 63°C, and the reaction time is 150s; the reaction equation is as follows:
[0040]
[0041] (2) After the reaction, the gas-liquid separation is carried out first, and the nitrogen oxides in the gas phase are further oxidized and then returned to the system to participate in the reaction again; the liquid phase is allowed to stand for stratification, the organic phase is crude mononitrotoluene, and the water phase is ...
PUM
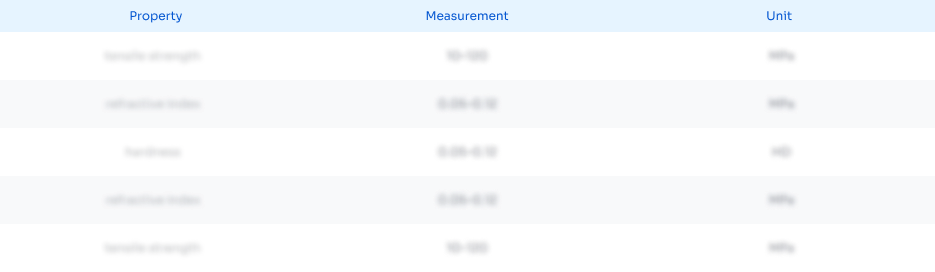
Abstract
Description
Claims
Application Information

- R&D
- Intellectual Property
- Life Sciences
- Materials
- Tech Scout
- Unparalleled Data Quality
- Higher Quality Content
- 60% Fewer Hallucinations
Browse by: Latest US Patents, China's latest patents, Technical Efficacy Thesaurus, Application Domain, Technology Topic, Popular Technical Reports.
© 2025 PatSnap. All rights reserved.Legal|Privacy policy|Modern Slavery Act Transparency Statement|Sitemap|About US| Contact US: help@patsnap.com