Piezoelectric ceramic-based high-precision electric spindle loading mechanism
A piezoelectric ceramic and loading mechanism technology, which is applied in the testing of mechanical components, testing of machine/structural components, measuring devices, etc., can solve the problem of low loading efficiency, inconvenient operation and movement of dynamometers, and difficult to guarantee the loading stress of electric spindle Accuracy requirements and other issues, to achieve the effect of convenient operation and movement, improve loading efficiency, and improve loading accuracy
- Summary
- Abstract
- Description
- Claims
- Application Information
AI Technical Summary
Problems solved by technology
Method used
Image
Examples
Embodiment Construction
[0019] The present invention will be further described in detail below in conjunction with the accompanying drawings and specific embodiments.
[0020] Such as Figure 1~4 As shown, a high-precision electric spindle loading mechanism based on piezoelectric ceramics includes a loading assembly and an adjustment assembly, and the loading assembly is installed on the adjustment assembly; the loading assembly includes a reaction support cylinder 1, a stress loading cylinder 2 and a piezoelectric Ceramic 3; the reaction force supporting cylinder 1 is set outside the stress loading cylinder 2, and the stress loading cylinder 2 has axial movement freedom in the reaction force supporting cylinder 1; the piezoelectric ceramic 3 is connected to the reaction force supporting cylinder 1 Between the inner surface of the bottom and the outer surface of the bottom of the stress-loading cylinder 2; the mouth of the stress-loading cylinder 2 adopts an arc surface structure, and the radian of t...
PUM
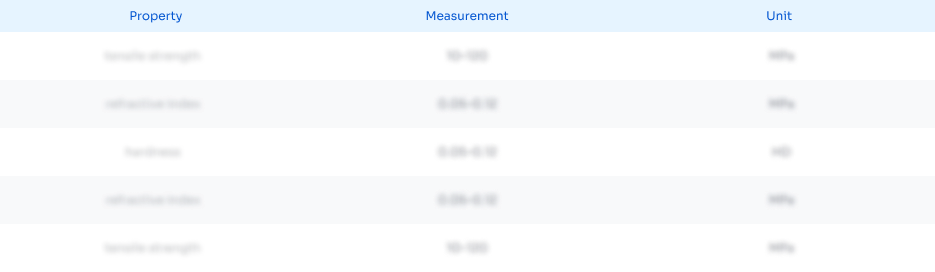
Abstract
Description
Claims
Application Information

- R&D Engineer
- R&D Manager
- IP Professional
- Industry Leading Data Capabilities
- Powerful AI technology
- Patent DNA Extraction
Browse by: Latest US Patents, China's latest patents, Technical Efficacy Thesaurus, Application Domain, Technology Topic, Popular Technical Reports.
© 2024 PatSnap. All rights reserved.Legal|Privacy policy|Modern Slavery Act Transparency Statement|Sitemap|About US| Contact US: help@patsnap.com