Forging equipment for small hardware production
A technology for small hardware and equipment, applied in the field of forging equipment for small hardware production, can solve the problems of difficulty in ensuring consistent rotation angles, insufficient safety, etc., and achieve the effects of sufficient forging, strong adaptability, and improved forging efficiency.
- Summary
- Abstract
- Description
- Claims
- Application Information
AI Technical Summary
Problems solved by technology
Method used
Image
Examples
Embodiment 1
[0021] see Figure 1~2 , in an embodiment of the present invention, a forging equipment for hardware production, including a base plate 1, a workbench 19 and a forging hammer 13, support legs 21 are installed on the bottom four corners of the base plate 1, and a mounting frame is fixed on the base plate 1 12. A workbench 19 is installed on one side of the upper surface of the base plate 1 through a fixed rod 20, a forging hammer 13 is arranged above the workbench 19, a screw rod 22 is set between the base plate 1 and the workbench 19, and the screw rod 22 passes through the bearing and the mounting plate Rotate and install on the base plate, the right end of the screw rod 22 is fixedly connected with the output shaft of the first motor 2 through a coupling, the first motor 2 is mounted on the mounting plate by screws, and the screw rod 22 is provided with a movable seat 3 on the outside. Rod 22 is threadedly connected with movable seat 3, and both sides of movable seat 3 botto...
Embodiment 2
[0023] see image 3 The difference between this embodiment and Embodiment 1 is that a sleeve 24 is sleeved on the outside of the rotating rod 17, and the sleeve 24 is fixedly connected with the rotating rod 17 through a fastening bolt 25, and the second cylindrical pin 16 is fixed by welding On the sleeve 24, the movable seat 3 includes a first seat body 26 and a second seat body 27, the first seat body 26 is located directly above the second seat body 27, and the screw rod 22 passes through the second seat body 27 And threaded with it, the second base body 27 both sides are all pierced with threaded rod 28, the threaded rod 28 is threaded with the second base body 27, the top of the threaded rod 28 is rotatably connected with the first base body 26 through the bearing, by rotating Threaded rod 28, so as to be able to adjust the height of the first seat 26, so that when forging workpieces of different thicknesses, they can be highly matched with the workbench 19, and when forg...
PUM
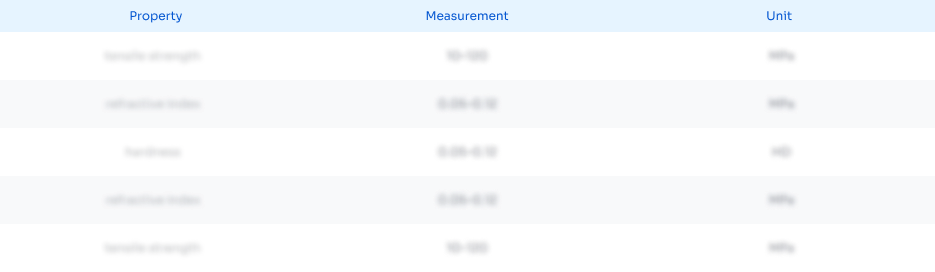
Abstract
Description
Claims
Application Information

- R&D
- Intellectual Property
- Life Sciences
- Materials
- Tech Scout
- Unparalleled Data Quality
- Higher Quality Content
- 60% Fewer Hallucinations
Browse by: Latest US Patents, China's latest patents, Technical Efficacy Thesaurus, Application Domain, Technology Topic, Popular Technical Reports.
© 2025 PatSnap. All rights reserved.Legal|Privacy policy|Modern Slavery Act Transparency Statement|Sitemap|About US| Contact US: help@patsnap.com