Target material manufacturing method
A manufacturing method and target material technology, which is applied in the direction of manufacturing tools, metal rolling, metal rolling, etc., can solve the problems that the sputtering performance of the target material needs to be improved, and achieve the effect of small stress accumulation and moderate deformation rate of upsetting thickness
- Summary
- Abstract
- Description
- Claims
- Application Information
AI Technical Summary
Problems solved by technology
Method used
Image
Examples
Embodiment Construction
[0031] It can be seen from the background art that the sputtering performance of existing targets needs to be improved.
[0032] Now combine with a target manufacturing method for analysis. The target manufacturing method is as follows: providing a forged tantalum target, the forged tantalum target including a sputtering surface; rolling the forged tantalum target by using a rolling process, so that the forged tantalum target is vertical to the The rolling thickness deformation rate in the direction of the sputtering surface is 80% to 90%, forming a finished tantalum target.
[0033] The finished tantalum target produced by the above method has poor sputtering performance.
[0034] The rolling thickness deformation rate of the forged tantalum target is large, and the direction of the forged tantalum target subjected to the rolling force is mainly perpendicular to the sputtering surface, so that the stress accumulation in the forged tantalum target perpendicular to the sputter...
PUM
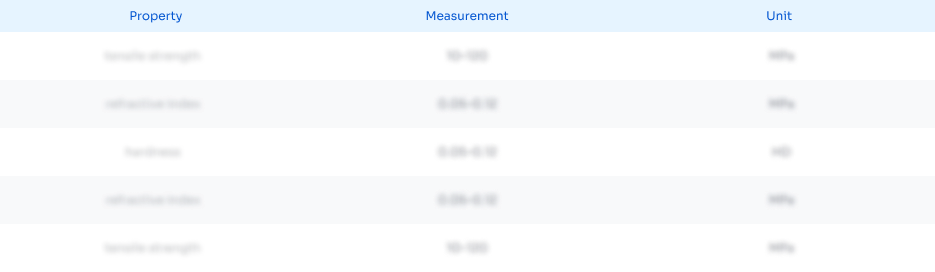
Abstract
Description
Claims
Application Information

- Generate Ideas
- Intellectual Property
- Life Sciences
- Materials
- Tech Scout
- Unparalleled Data Quality
- Higher Quality Content
- 60% Fewer Hallucinations
Browse by: Latest US Patents, China's latest patents, Technical Efficacy Thesaurus, Application Domain, Technology Topic, Popular Technical Reports.
© 2025 PatSnap. All rights reserved.Legal|Privacy policy|Modern Slavery Act Transparency Statement|Sitemap|About US| Contact US: help@patsnap.com