Cold annealing and pickling technique for 204 Cu stainless steel with thickness of 1.5-2.0 mm
A stainless steel, cold-rolled annealing technology, applied in the direction of manufacturing tools, furnace types, furnaces, etc., can solve the problems of uneven surface oxide scale, residual oxide scale, and uneven oxide scale on the surface of strip steel, so as to improve the surface quality of products , Improve the effect of brush roller mode and reduce the reference temperature
- Summary
- Abstract
- Description
- Claims
- Application Information
AI Technical Summary
Problems solved by technology
Method used
Image
Examples
Embodiment 1
[0032] 1.5-2.0mm thick 204Cu stainless steel cold annealing and pickling process, including cold rolling annealing step and mixed pickling step, cold rolling annealing step Z1, Z2, Z3, Z4, Z5, Z6, There are 10 heating zones Z7, Z8, Z9, Z10 and different temperatures are set. The temperature reference (°C) is as follows:
[0033]
[0034] In the table: TV=thickness of strip steel×running speed of strip steel, Kvar—represents the increased temperature value for every increase of 1 TV value.
[0035] The setting of the brush roller in the mixed acid pickling step is as follows:
[0036] parameter
1# brush roller
2# brush roller
3# brush roller
4# brush roller
Current (A)
15.4
15.4
10.7
10.7
speed(rmp)
600
600
600
600
Load(mm)
2
2
2
2
[0037] The material of the brush roller in this embodiment is nylon.
[0038] The neutral salt electrolysis benchmark in the neutral salt electrolysis step...
Embodiment 2
[0044] 1.5-2.0mm thick 204Cu stainless steel cold annealing and pickling process, including cold rolling annealing step and mixed pickling step, cold rolling annealing step Z1, Z2, Z3, Z4, Z5, Z6, There are 10 heating zones Z7, Z8, Z9, Z10 and different temperatures are set. The temperature reference (°C) is as follows:
[0045]
[0046] In the table: TV=strip thickness×strip running speed, Kvar—represents the increased temperature value for every increase of 1 TV value;
[0047] The setting of the brush roller in the mixed acid pickling step is as follows:
[0048]
[0049] The material of the brush roller in this embodiment is nylon.
[0050] The neutral salt electrolysis benchmark in the neutral salt electrolysis step is as follows:
[0051]
[0052] The mixed acid standard in the mixed acid pickling step is as follows:
[0053]
[0054] The 204Cu stainless steel plate with a thickness of 1.5-2.0mm was obtained through the steps set in the above-mentioned Ex...
Embodiment 3
[0056] 1.5-2.0mm thick 204Cu stainless steel cold annealing and pickling process, including cold rolling annealing step and mixed pickling step, cold rolling annealing step Z1, Z2, Z3, Z4, Z5, Z6, There are 10 heating zones Z7, Z8, Z9, Z10 and different temperatures are set. The temperature reference (°C) is as follows:
[0057]
[0058] In the table: TV=thickness of strip steel×running speed of strip steel, Kvar—represents the increased temperature value for every increase of 1 TV value.
[0059] The setting of the brush roller in the mixed acid pickling step is as follows:
[0060]
[0061] The material of the brush roller in this embodiment is nylon.
[0062] The neutral salt electrolysis benchmark in the neutral salt electrolysis step is as follows:
[0063]
[0064] The mixed acid standard in the mixed acid pickling step is as follows:
[0065]
[0066] The 204Cu stainless steel plate with a thickness of 1.5-2.0 mm was obtained through the steps set in the...
PUM
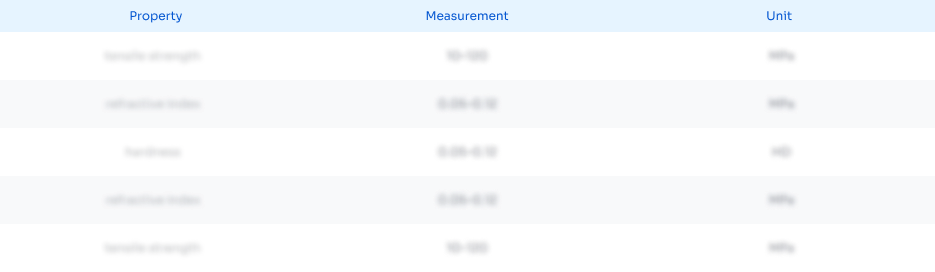
Abstract
Description
Claims
Application Information

- R&D
- Intellectual Property
- Life Sciences
- Materials
- Tech Scout
- Unparalleled Data Quality
- Higher Quality Content
- 60% Fewer Hallucinations
Browse by: Latest US Patents, China's latest patents, Technical Efficacy Thesaurus, Application Domain, Technology Topic, Popular Technical Reports.
© 2025 PatSnap. All rights reserved.Legal|Privacy policy|Modern Slavery Act Transparency Statement|Sitemap|About US| Contact US: help@patsnap.com