Method and device for testing function of refining of fusion metal grains through ultrasonic waves
A molten metal, grain refinement technology, applied in the field of ultrasonic cavitation, can solve problems such as uneven deformation, experimental result error, waste, etc., and achieve the effect of saving experimental operation time and experimental workload
- Summary
- Abstract
- Description
- Claims
- Application Information
AI Technical Summary
Problems solved by technology
Method used
Image
Examples
Embodiment Construction
[0026] Such as figure 1 As shown, a device for testing the effect of ultrasonic waves on the refinement of molten metal grains, including a single-chip microcomputer 4, an ultrasonic pulse receiver 2, an ultrasonic probe A1, an ultrasonic probe A2, an ultrasonic probe A3, an ultrasonic probe A4, and an ultrasonic probe A5 And the heating device 9, the single-chip microcomputer 4 is connected with the ultrasonic pulse generating receiver 2 through wires, the ultrasonic pulse generating receiver 2 is connected with the ultrasonic probe A through the multi-directional joint 6, and the alloy 8 is placed on the heating device 9. The heating device 9 places the alloy in a direction facing the ultrasonic probes A1 , A2 , A3 , A4 , A5 .
[0027] The single-chip microcomputer 3 is connected with the host computer 5 through the USB bus.
[0028] The device also includes a holding device 7, which is arranged above the heating device 9, and several grooves are provided on the holding dev...
PUM
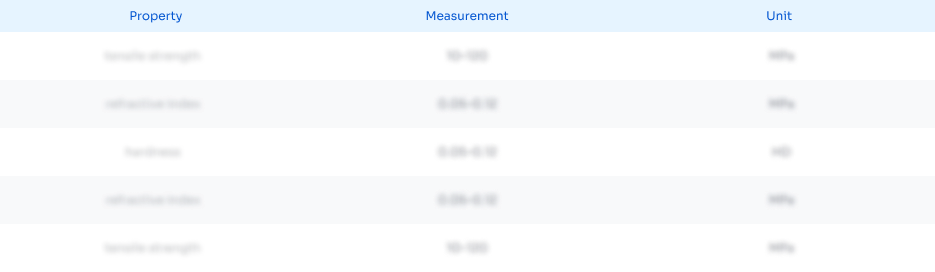
Abstract
Description
Claims
Application Information

- Generate Ideas
- Intellectual Property
- Life Sciences
- Materials
- Tech Scout
- Unparalleled Data Quality
- Higher Quality Content
- 60% Fewer Hallucinations
Browse by: Latest US Patents, China's latest patents, Technical Efficacy Thesaurus, Application Domain, Technology Topic, Popular Technical Reports.
© 2025 PatSnap. All rights reserved.Legal|Privacy policy|Modern Slavery Act Transparency Statement|Sitemap|About US| Contact US: help@patsnap.com