A molding process of felt built-in support
A molding process and felt technology, which is applied in the field of molding technology with built-in felt brackets, can solve the problems of high scrap rate of parts, inability to ensure consistency, exposed parts brackets, etc., to save labor costs, speed up production cycle, and high installation accuracy Effect
- Summary
- Abstract
- Description
- Claims
- Application Information
AI Technical Summary
Problems solved by technology
Method used
Image
Examples
Embodiment
[0034] The existing felt forming process such as figure 1 with figure 2 As shown, the device used is a blow mold 1 and a molding mold connected by a transmission belt 2; the molding mold includes an upper mold 31 and a lower mold 32. Firstly, the felt blank is formed into the required rough shape in the blow molding mold 1, and then sent into the forming mold through the conveyor belt, and the workers tear off part of the felt blank in the area where the plastic bracket needs to be placed, and place the plastic bracket manually, and then place it on the surface of the bracket separately A layer of felt is covered, and then the forming mold is cooled and formed to obtain a felt, and finally the felt is punched into a punching die to obtain a sound insulation mat product.
[0035] The present invention is a molding process of a felt built-in bracket, which adopts a blow molding device such as image 3 , Figure 4 with Figure 5 As shown, the blow mold 1 and the forming mold...
PUM
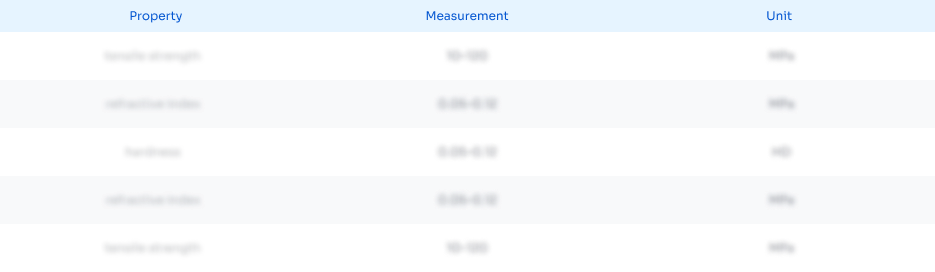
Abstract
Description
Claims
Application Information

- R&D
- Intellectual Property
- Life Sciences
- Materials
- Tech Scout
- Unparalleled Data Quality
- Higher Quality Content
- 60% Fewer Hallucinations
Browse by: Latest US Patents, China's latest patents, Technical Efficacy Thesaurus, Application Domain, Technology Topic, Popular Technical Reports.
© 2025 PatSnap. All rights reserved.Legal|Privacy policy|Modern Slavery Act Transparency Statement|Sitemap|About US| Contact US: help@patsnap.com