Method for removing shrinkage cavity and loosening of master alloy bar in vacuum smelting
A vacuum smelting and master alloy technology, applied in the field of smelting, can solve the problems of shrinkage cavity depth, reduce shrinkage cavity depth, and can not get the surrounding metal liquid replenishment, etc., to achieve the effect of dense internal structure and increased fluidity
- Summary
- Abstract
- Description
- Claims
- Application Information
AI Technical Summary
Problems solved by technology
Method used
Image
Examples
Embodiment 1
[0037] (1) Name of smelting alloy: K418.
[0038] (2) Ingredients: Dosing and loading according to the calculated ingredient list.
[0039] (3) Preparatory work for smelting: 1) The smelting crucible is made of magnesium or aluminum forming crucible;
[0040] 2) The crucible is baked and furnace-washed, and the furnace-washing process uses pure nickel or the returned material of the same steel type to wash the furnace;
[0041] 3) Baking of raw materials: Toasting and degassing the above-mentioned raw materials of Ni, Co, Cr, W and Mo respectively;
[0042] 4) Baking of refractory materials: the funnel brick and the splitter brick are respectively baked at 400°C for 2 hours;
[0043] 5) In the ingot casting room of the vacuum induction furnace, the casting mold is heated by a ring heating furnace, and the heating temperature of the casting mold is 600°C.
[0044] (4) Vacuum smelting: Melting alloy raw materials in a melting crucible under the condition of vacuum degree <4Pa...
Embodiment 2
[0048] (1) Name of smelting alloy: K418.
[0049] (2) Ingredients: Dosing and loading according to the calculated ingredient list.
[0050] (3) Preparatory work for smelting: 1) The smelting crucible is made of magnesium or aluminum forming crucible;
[0051] 2) The crucible is baked and furnace-washed, and the furnace-washing process uses pure nickel or the returned material of the same steel type to wash the furnace;
[0052] 3) Baking of raw materials: Toasting and degassing the above-mentioned raw materials of Ni, Co, Cr, W and Mo respectively;
[0053] 4) Baking of refractory materials: the funnel brick and the splitter brick are respectively baked at 400°C for 2 hours;
[0054] 5) In the ingot casting room of the vacuum induction furnace, the casting mold is heated by a ring heating furnace, and the heating temperature of the casting mold is 620°C.
[0055] (4) Vacuum smelting: Melting alloy raw materials in a melting crucible under the condition of vacuum degree <4Pa...
Embodiment 3
[0059] (1) Name of smelting alloy: K418.
[0060] (2) Ingredients: Dosing and loading according to the calculated ingredient list.
[0061] (3) Preparatory work for smelting: 1) The smelting crucible is made of magnesium or aluminum forming crucible;
[0062] 2) The crucible is baked and furnace-washed, and the furnace-washing process uses pure nickel or the returned material of the same steel type to wash the furnace;
[0063] 3) Baking of raw materials: Toasting and degassing the above-mentioned raw materials of Ni, Co, Cr, W and Mo respectively;
[0064] 4) Baking of refractory materials: the funnel brick and the splitter brick are respectively baked at 400°C for 2 hours;
[0065] 5) In the ingot casting chamber of the vacuum induction furnace, the casting mold is heated by a ring heating furnace, and the heating temperature of the casting mold is 650°C.
[0066] (4) Vacuum smelting: Melting alloy raw materials in a melting crucible under the condition of vacuum degree <...
PUM
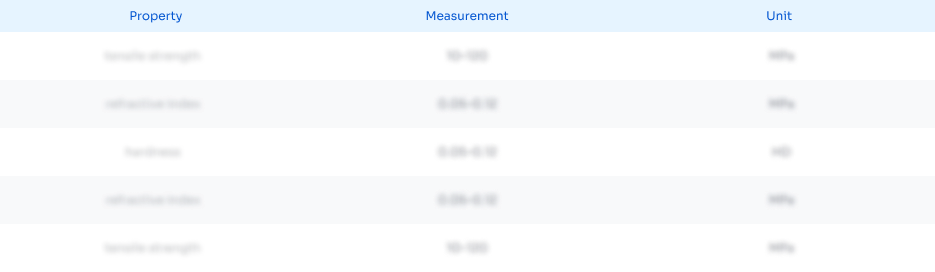
Abstract
Description
Claims
Application Information

- R&D
- Intellectual Property
- Life Sciences
- Materials
- Tech Scout
- Unparalleled Data Quality
- Higher Quality Content
- 60% Fewer Hallucinations
Browse by: Latest US Patents, China's latest patents, Technical Efficacy Thesaurus, Application Domain, Technology Topic, Popular Technical Reports.
© 2025 PatSnap. All rights reserved.Legal|Privacy policy|Modern Slavery Act Transparency Statement|Sitemap|About US| Contact US: help@patsnap.com