Anti-corrosion aqueous paint and preparation method thereof
A water-based coating and modification technology, applied in the direction of anti-corrosion coatings, coatings, etc., can solve the problems of non-conversion, anti-flash corrosion performance, poor salt spray resistance, etc., to achieve easy damage, enhanced corrosion inhibition and rust resistance. , the effect of contact reduction
- Summary
- Abstract
- Description
- Claims
- Application Information
AI Technical Summary
Problems solved by technology
Method used
Image
Examples
preparation example Construction
[0029] A preparation method for anti-corrosion water-based paint, comprising the steps of:
[0030] S1. Take the anti-flash corrosion additive according to the mass ratio of 8~10:1~3:1~3, add OP-10 and sodium lauryl sulfate, raise the temperature to 55~60°C, and then add the anti-flash corrosion additive with a mass ratio of 8~15 times of deionized water, stirred and mixed at 5000r / min for 20~40min to obtain the mixture, in parts by mass, take 5~10 parts of the mixture, 5~8 parts of glyceryl methacrylate, 2~5 parts of methyl methacrylate ester, 2~4 parts of n-butyl acrylate, 1~3 parts of styrene, 8~10 parts of acrylic acid, stirred and mixed at 55~60°C for 1~3h to obtain the matrix;
[0031]S2. In parts by mass, take 3~5 parts of OP-10, 1~3 parts of sodium lauryl sulfate, 8~10 parts of sodium bicarbonate, 5~9 parts of rust-removing activator, 10~15 parts of modified Sexual active agent, 80~100 parts of deionized water, stirring and mixing at 55~65°C for 30~40min to obtain the...
Embodiment 1
[0033] Rust conversion active agent: (1) Take 1,2-propanediol and add itaconic acid at a mass ratio of 3:4, heat up to 70°C and stir for 20 minutes, then add p-toluenesulfonic acid with 3% itaconic acid mass, and heat at 70°C Insulate for 1 hour, then raise the temperature to 105°C, stir and mix for 2 hours, and cool to room temperature to obtain the rust-transforming active agent.
[0034] Anti-flash corrosion additive: Take β-hydroxyethyl methacrylate and add deionized water at a mass ratio of 2:8, add hydroquinone with 10% deionized water quality, stir and mix at 35°C for 30min, then add deionized water The mass of 10% phosphorus pentoxide was heated to 70°C and stirred for 2 hours to obtain a stirred mixture. The stirred mixture was added to deionized water at a mass ratio of 2:10, heated to 85°C and stirred for 1 hour, cooled to room temperature to obtain an anti-flash corrosion additives.
[0035] Modified active agent: take aniline and add p-phenylenediamine and OP-10 ...
Embodiment 2
[0040] Rust conversion active agent: (1) Take 1,2-propanediol and add itaconic acid at a mass ratio of 5:7, heat up to 73°C and mix for 25 minutes, then add p-toluenesulfonic acid with 4% itaconic acid mass, and heat at 73°C Insulate for 2 hours, then raise the temperature to 108°C, stir and mix for 3 hours, and cool to room temperature to obtain the rust-transforming active agent.
[0041] Anti-flash corrosion additive: Take β-hydroxyethyl methacrylate and add deionized water at a mass ratio of 3:9, add hydroquinone with 13% deionized water quality, stir and mix at 38°C for 40min, then add deionized water Phosphorus pentoxide with a mass of 18% was heated up to 73°C and stirred for 3 hours to obtain a stirred mixture. Take the stirred mixture and add deionized water at a mass ratio of 3:13, heat up to 88°C and stir for 2 hours, and cool to room temperature to obtain an anti-flash corrosion additives.
[0042] Modified active agent: take aniline and add p-phenylenediamine and...
PUM
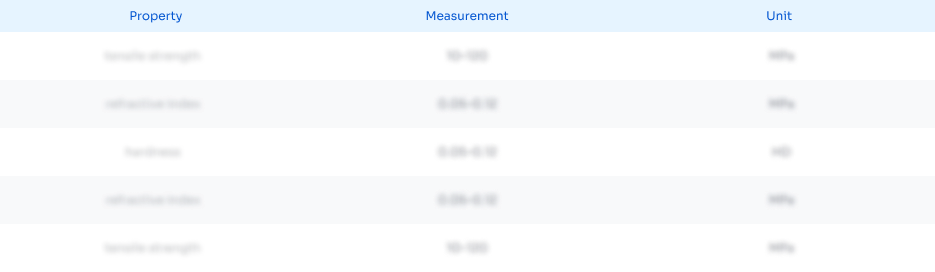
Abstract
Description
Claims
Application Information

- Generate Ideas
- Intellectual Property
- Life Sciences
- Materials
- Tech Scout
- Unparalleled Data Quality
- Higher Quality Content
- 60% Fewer Hallucinations
Browse by: Latest US Patents, China's latest patents, Technical Efficacy Thesaurus, Application Domain, Technology Topic, Popular Technical Reports.
© 2025 PatSnap. All rights reserved.Legal|Privacy policy|Modern Slavery Act Transparency Statement|Sitemap|About US| Contact US: help@patsnap.com