Method for production of acid from phosphogypsum by utilizing electrolytic-aluminium waste cathode carbon blocks
A waste cathode carbon block, phosphogypsum technology, applied in chemical instruments and methods, inorganic chemistry, cement production and other directions, can solve the problems of inability to achieve strict temperature control, energy waste, secondary pollution, etc., and achieve saving and anti-leakage treatment. and other costs, the economic and environmental benefits are obvious, and the effect of eliminating the impact of the environment
- Summary
- Abstract
- Description
- Claims
- Application Information
AI Technical Summary
Problems solved by technology
Method used
Examples
Embodiment 1
[0030] Put the phosphogypsum into the hammer dryer, disperse and dry it, and dehydrate it into hemihydrate gypsum; mechanically crush the waste cathode carbon block sorted from the waste residue generated by the overhaul of the electrolytic cell into powder; mix hemihydrate gypsum, clay, The bauxite and electrolytic aluminum waste cathode carbon block powder are mixed and then dried online. After drying, they enter the integrated grinding system for integrated grinding to obtain phosphogypsum cement raw meal. The ratio of C to S in the raw meal is 0.5; put the phosphogypsum cement raw meal into the secondary cyclone preheater, preheat it in nitrogen atmosphere, carry out the primary preheating of the phosphogypsum cement raw meal, raise the temperature of the raw meal to 255°C, and keep it warm for 30min; The gypsum cement raw meal is preheated in the second stage, the temperature of the raw meal is raised to 450 ° C, and the temperature is kept for 30 minutes; the preheated ph...
Embodiment 2
[0032] Put the phosphogypsum into the hammer dryer, disperse and dry it, and dehydrate it into hemihydrate gypsum; mechanically crush the waste cathode carbon block sorted from the waste residue generated by the overhaul of the electrolytic cell into powder; mix hemihydrate gypsum, clay, The bauxite and electrolytic aluminum waste cathode carbon block powder are mixed and then dried online. After drying, they enter the integrated grinding system for integrated grinding to obtain phosphogypsum cement raw meal. The ratio of C to S in the raw meal is 1. Put the phosphogypsum cement raw meal into the secondary cyclone preheater, preheat it in nitrogen atmosphere, carry out the primary preheating on the phosphogypsum cement raw meal, raise the temperature of the raw meal to 350°C, and keep it warm for 45 minutes; The gypsum cement raw meal is preheated in the second stage, the temperature of the raw meal is raised to 750°C, and it is kept for 45 minutes; the preheated phosphogypsum ...
Embodiment 3
[0034]Put the phosphogypsum into the hammer dryer, disperse and dry it, and dehydrate it into hemihydrate gypsum; mechanically crush the waste cathode carbon block sorted from the waste residue generated by the overhaul of the electrolytic cell into powder; hemihydrate gypsum, clay, The bauxite and electrolytic aluminum waste cathode carbon block powder are mixed and then dried online. After drying, they enter the integrated grinding system for integrated grinding to obtain phosphogypsum cement raw meal. The ratio of C to S in the raw meal is 2. Put the phosphogypsum cement raw meal into the secondary cyclone preheater and preheat it in a nitrogen atmosphere, and perform primary preheating on the phosphogypsum cement raw meal, raise the temperature of the raw meal to 450°C and keep it warm for 1 hour; The gypsum cement raw meal is preheated in two stages, the temperature of the raw meal is raised to 780°C, and it is kept for 1 hour; the preheated phosphogypsum cement raw meal i...
PUM
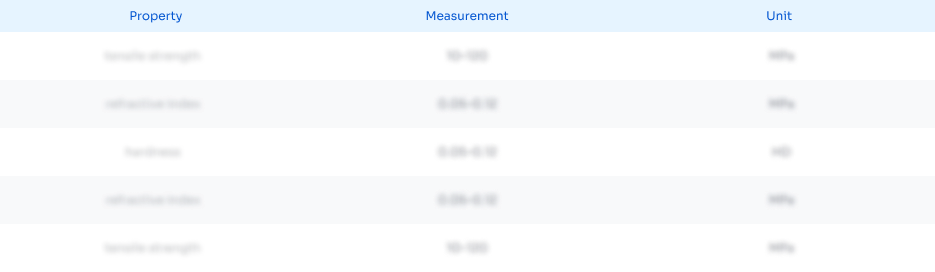
Abstract
Description
Claims
Application Information

- R&D
- Intellectual Property
- Life Sciences
- Materials
- Tech Scout
- Unparalleled Data Quality
- Higher Quality Content
- 60% Fewer Hallucinations
Browse by: Latest US Patents, China's latest patents, Technical Efficacy Thesaurus, Application Domain, Technology Topic, Popular Technical Reports.
© 2025 PatSnap. All rights reserved.Legal|Privacy policy|Modern Slavery Act Transparency Statement|Sitemap|About US| Contact US: help@patsnap.com