A shell-making process for easily collapsible shells
A collapsing and crafting technology, applied in the field of shell making process of easily collapsible shells, to achieve the effect of reducing the number of layers, reducing production costs and high dimensional accuracy
- Summary
- Abstract
- Description
- Claims
- Application Information
AI Technical Summary
Problems solved by technology
Method used
Image
Examples
Embodiment Construction
[0028] In order to make the object, technical solution and advantages of the present invention clearer, the present invention will be further described in detail below in conjunction with the accompanying drawings and embodiments. It should be understood that the specific embodiments described here are only used to explain the present invention, not to limit the present invention.
[0029] Such as figure 1 , 2 Shown, a kind of manufacturing process of metal casting mold shell, specifically produce a kind of metal casting with holes, comprising the following steps:
[0030] A wax model 1 and a wax die head 2 of the metal casting are pressed by a mold, and several wax models 1 are assembled on the wax die head 2 to form a group tree; and then the group tree is cleaned with a release agent.
[0031] Slurry, sanding and air-drying operations were performed on the wax model 1 for several times, among which:
[0032] For the first time, the zircon slurry made by mixing silica sol...
PUM
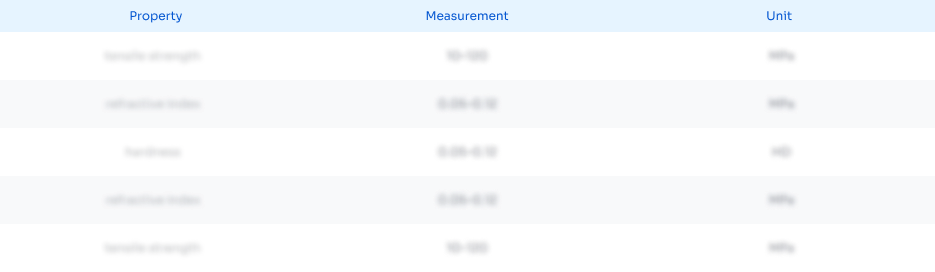
Abstract
Description
Claims
Application Information

- R&D Engineer
- R&D Manager
- IP Professional
- Industry Leading Data Capabilities
- Powerful AI technology
- Patent DNA Extraction
Browse by: Latest US Patents, China's latest patents, Technical Efficacy Thesaurus, Application Domain, Technology Topic, Popular Technical Reports.
© 2024 PatSnap. All rights reserved.Legal|Privacy policy|Modern Slavery Act Transparency Statement|Sitemap|About US| Contact US: help@patsnap.com