Sintering process method applicable to low-pressure bead sintering of double furnace
A technology of low-pressure sintering and process method, which is applied in the production field of diamond beads, which can solve problems such as inconsistent heating curves of beads, influence of physical properties of bead matrix, and large fluctuations in bead quality, so as to achieve stable product quality, simple operation, and uniform temperature Effect
- Summary
- Abstract
- Description
- Claims
- Application Information
AI Technical Summary
Problems solved by technology
Method used
Image
Examples
Embodiment Construction
[0015] The technical solutions of the present invention will be further described below in conjunction with the embodiments shown in the accompanying drawings.
[0016] The present invention is applicable to the sintering process method of double-body furnace low-pressure sintering beading, is in such as figure 1 It is implemented in the double-body furnace 1 of the original sintering beads shown, and its embodiment is:
[0017] 1. Three sets of supplementary heat temperature-controlled heating modules 3 are respectively installed at the upper, middle and lower positions of the center of the furnace 2 of the double-body furnace 1, that is, the three sets of supplementary heat temperature-controlled heating modules 3 are formed into components and inserted into the furnace 2 (circular furnace In the center of the area surrounded by the wall), the height positions of the three sets of supplementary heating temperature-controlled heating modules 3 correspond to the upper, middle ...
PUM
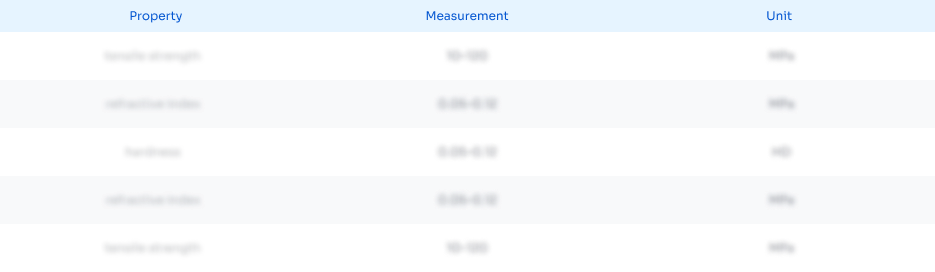
Abstract
Description
Claims
Application Information

- Generate Ideas
- Intellectual Property
- Life Sciences
- Materials
- Tech Scout
- Unparalleled Data Quality
- Higher Quality Content
- 60% Fewer Hallucinations
Browse by: Latest US Patents, China's latest patents, Technical Efficacy Thesaurus, Application Domain, Technology Topic, Popular Technical Reports.
© 2025 PatSnap. All rights reserved.Legal|Privacy policy|Modern Slavery Act Transparency Statement|Sitemap|About US| Contact US: help@patsnap.com