A low reaction temperature, low-deterioration wire mesh catalyst manufacturing process
A reaction temperature, wire mesh technology, applied in catalyst activation/preparation, physical/chemical process catalysts, chemical instruments and methods, etc., can solve the problem of high reaction temperature and low reaction temperature. Fast and other problems, to achieve the effect of reducing the reaction working temperature, reducing the specific surface area, and reducing the deterioration coefficient
- Summary
- Abstract
- Description
- Claims
- Application Information
AI Technical Summary
Problems solved by technology
Method used
Image
Examples
Embodiment 1
[0014] 1. The size of the wire mesh carrier is 34*30*10, the mass ratio of the precious metal is Pt:Pd:Rh=0:20:1, and the mass concentration of the precious metal coating solution is 50g / ft 3 ;
[0015] 2. Dilute the above precious metal coating solution to 30g / ft 3 , added to the coating to form a slurry, wherein the composition of the coating is alumina powder, cerium-zirconium, precious metals, and adhesives. The precious metal accounts for 0.01% of the total mass of the slurry, and then evenly coated on the wire mesh for normal After drying, roast at 550±50°C and cool naturally for use;
[0016] 3. The semi-finished wire mesh catalytic converter after cooling is subjected to pre-aging treatment at 950±50°C for 4 hours, and then cooled naturally for use;
[0017] 4. Dilute the precious metal coating solution in step 1 to 20g / ft 3 Precious metal solution, forming a surface layer coating liquid, stand-by, wherein the mass ratio of the amount of precious metal contained in ...
Embodiment 2
[0020] The method used in Example 2 is similar to that of Example 1, except that the mass ratio of the amount of noble metal contained in the surface coating liquid in step 4 to the amount of noble metal contained in the slurry in step 2 is 2:8.
PUM
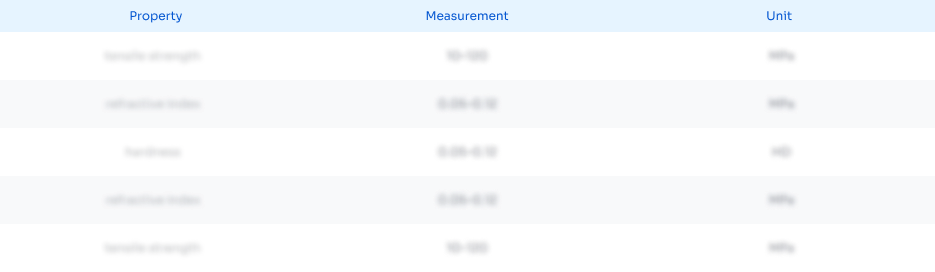
Abstract
Description
Claims
Application Information

- R&D
- Intellectual Property
- Life Sciences
- Materials
- Tech Scout
- Unparalleled Data Quality
- Higher Quality Content
- 60% Fewer Hallucinations
Browse by: Latest US Patents, China's latest patents, Technical Efficacy Thesaurus, Application Domain, Technology Topic, Popular Technical Reports.
© 2025 PatSnap. All rights reserved.Legal|Privacy policy|Modern Slavery Act Transparency Statement|Sitemap|About US| Contact US: help@patsnap.com