Method for preparing chitosan fiber paper-based material based on wet paper-making technology
A technology of chitosan fiber and technology, applied in fiber raw material treatment, pulp beating method, cellulose pulp post-treatment, etc., can solve the problems of incapable of large-scale continuous production, complex operation, etc., and achieve easy modification, good safety, The effect of splitting is obvious
- Summary
- Abstract
- Description
- Claims
- Application Information
AI Technical Summary
Problems solved by technology
Method used
Image
Examples
Embodiment 1
[0036] First, cut 30 grams of chitosan fibers into lengths of 3mm-5mm, disperse them in water and absorb water for 5 hours in the form of a suspension, and then use a PFI mill to beat them at 8000 rpm when the dryness is 10 wt%. The good pulp fiber is dispersed into a pulp suspension with a concentration of 0.06 wt% by adding deionized water, and after being fully dispersed, sheet forming is carried out on a manual paper sheet machine, and the formed wet paper web is transferred to the press operation table Cover the dry filter paper for roll dehydration treatment, and then transfer the dehydrated wet paper web to a dryer at 90°C for 20 minutes to obtain chitosan fiber paper-based materials, with a weight of 110g / m 2 . The prepared chitosan fiber paper-based material is shown in Figure 1. After the chitosan fiber is beaten, the fiber is finely divided and part of the fiber is nanometerized to form a good fibrous porous structure.
Embodiment 2
[0038]First cut 30 grams of chitosan fibers into lengths of 10-30mm, then soak them in 0.05wt% sodium hydroxide solution for 8 hours, rinse the slurry with deionized water until the pH value of the slurry washing liquid is neutral. When the dryness is 10 wt%, the PFI mill is used to beat it at 20000 rpm, and the beaten pulp fiber is taken and deionized water is dispersed into a pulp suspension with a concentration of 1 wt%. Scatter on the manual sheet machine for sheet forming, transfer the formed wet paper web to the press operation table, cover the dry filter paper for roll dehydration, and then transfer the dehydrated wet paper web to the dryer at 90°C Dried for 20min, the obtained chitosan fiber paper-based material, quantitatively 110g / m 2 .
Embodiment 3
[0040] First cut 30 grams of chitosan fibers into lengths of 25mm-30mm, then absorb water in a 10wt% sodium hydroxide solution for 1 hour, and rinse the slurry with deionized water until the pH value of the slurry washing solution is neutral sex. When the dryness is 10 wt%, the PFI mill is used to beat it at 10000 rpm, and the beaten pulp fiber is dispersed with deionized water to form a slurry suspension with a concentration of 0.03 wt%. Dispersed on the paper sheet machine for sheet forming, transfer the formed wet paper web to the press operation table to cover the dry filter paper for roll dehydration, and then transfer the dehydrated wet paper web to the dryer at 80°C for drying 20min, get 100 g / m 2 Quantitative chitosan fiber paper base material.
[0041] The prepared chitosan fiber paper base material such as figure 2 As shown, the chitosan fiber after beating has good fiber separation, and some fibers are nano-sized, forming a good fibrous porous structure.
PUM
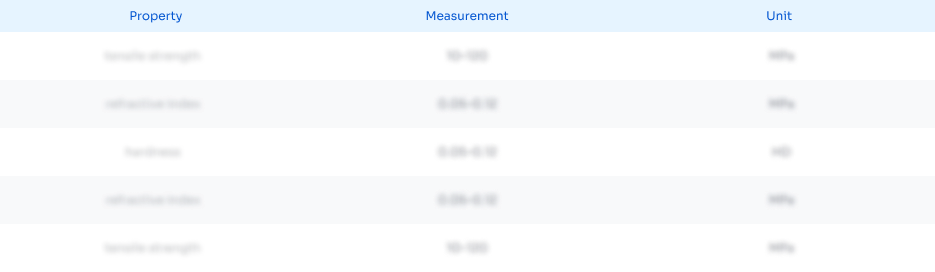
Abstract
Description
Claims
Application Information

- R&D
- Intellectual Property
- Life Sciences
- Materials
- Tech Scout
- Unparalleled Data Quality
- Higher Quality Content
- 60% Fewer Hallucinations
Browse by: Latest US Patents, China's latest patents, Technical Efficacy Thesaurus, Application Domain, Technology Topic, Popular Technical Reports.
© 2025 PatSnap. All rights reserved.Legal|Privacy policy|Modern Slavery Act Transparency Statement|Sitemap|About US| Contact US: help@patsnap.com