Forging method of titanium alloy ingot castings with large height-diameter ratio
A high-diameter ratio, titanium alloy technology, applied in the field of titanium alloy forging, can solve the problems of bending, folding, double drum, etc., to achieve the effect of high yield, solve double drum, and uniform composition and structure
- Summary
- Abstract
- Description
- Claims
- Application Information
AI Technical Summary
Problems solved by technology
Method used
Image
Examples
Embodiment 1
[0023] (1) The TC11 ingot of Φ660*2000mm was prepared by smelting three times in a vacuum consumable electric arc furnace;
[0024] (2) The TC11 ingot described in step (1) is forged into a square billet of □680mm by using the fast forging unit and the ingot billet die with a large height-to-diameter ratio; the deformation of the billet is controlled at 60%, and the deformation rate is Control at 20mm / s, preheat the mold before blank forging, the preheating temperature is ≥100℃;
[0025] (3) The billet completed in step (2) is subjected to 3 times of upsetting and drawing forging at 80°C above the β transformation temperature by using the rapid forging unit, and the deformation of each time is controlled at about 45%;
[0026] (4) The billet completed in step (3) is subjected to 4 times of upsetting and drawing forging at 50°C below the β transformation temperature by using the rapid forging unit, and the deformation of each time is controlled at about 40%, and the second fire...
Embodiment 2
[0029] (1) The TC6 ingot of Φ560*1800mm was prepared by smelting three times in a vacuum consumable electric arc furnace;
[0030] (2) The TC6 ingot described in step (1) is forged into a square billet of □580mm by using the quick forging unit and the ingot billet die with a large height-to-diameter ratio; the deformation of the billet is controlled at 65%, and the deformation rate Control at 18mm / s, preheat the mold before blank forging, the preheating temperature is ≥100℃;
[0031] (3) The billet completed in step (2) is subjected to upsetting and drawing forging for 3 times at 60°C above the β transformation temperature by using the rapid forging unit, and the deformation of each firing is controlled at about 45%;
[0032] (4) The billet completed in step (3) is subjected to 4 times of upsetting and drawing forging at 50°C below the β transformation temperature by using the rapid forging unit, and the deformation of each time is controlled at about 40%, and the second fire ...
PUM
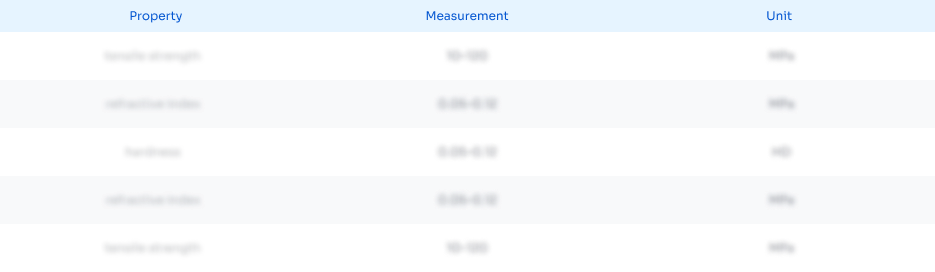
Abstract
Description
Claims
Application Information

- R&D
- Intellectual Property
- Life Sciences
- Materials
- Tech Scout
- Unparalleled Data Quality
- Higher Quality Content
- 60% Fewer Hallucinations
Browse by: Latest US Patents, China's latest patents, Technical Efficacy Thesaurus, Application Domain, Technology Topic, Popular Technical Reports.
© 2025 PatSnap. All rights reserved.Legal|Privacy policy|Modern Slavery Act Transparency Statement|Sitemap|About US| Contact US: help@patsnap.com