Method for plating copper and copper alloy coiled material with nickel
A copper alloy and coil technology, applied in the field of nickel plating on copper and copper alloy coils, can solve the problems of immaturity, inability to overcome the continuous electroplating process of coils, and the inability of production methods to meet customer requirements. solid effect
- Summary
- Abstract
- Description
- Claims
- Application Information
AI Technical Summary
Problems solved by technology
Method used
Examples
Embodiment Construction
[0022] In the prior art, the raw materials are stamped and then electroplated with nickel for monolithic shaped products.
[0023] The invention electroplates metal nickel on the surface of copper material through a special electroplating process, and forms a firmly bonded, semi-bright and bright, dense, uniform and continuous coating on the surface of copper or copper alloy. The surface of the electroplated copper or copper alloy has the characteristics of nickel and the advantages of copper, and can be widely used in components of electronic products such as mobile phones and computer communications.
[0024] In the method of the present invention, the electroplating of copper or copper alloy coils is carried out in a bath-type electroplating device. The tank-type electroplating device is made of very corrosion-resistant metal materials. The entire device is several meters or even tens of meters long. According to the needs of the electroplating process, the device is divide...
PUM
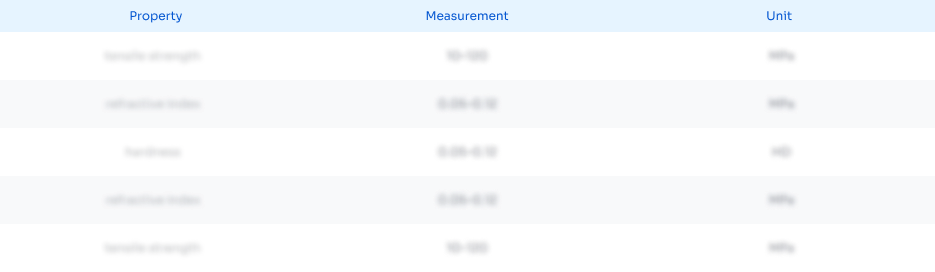
Abstract
Description
Claims
Application Information

- R&D
- Intellectual Property
- Life Sciences
- Materials
- Tech Scout
- Unparalleled Data Quality
- Higher Quality Content
- 60% Fewer Hallucinations
Browse by: Latest US Patents, China's latest patents, Technical Efficacy Thesaurus, Application Domain, Technology Topic, Popular Technical Reports.
© 2025 PatSnap. All rights reserved.Legal|Privacy policy|Modern Slavery Act Transparency Statement|Sitemap|About US| Contact US: help@patsnap.com