Smelting plant waste tailing treatment technology and equipment
A treatment process, smelter technology, applied in the improvement of process efficiency, cells, electrolysis process, etc., can solve the problems of small processing capacity, high operating cost, waste of resources, etc., achieve large processing capacity, avoid precipitation, and facilitate cleaning Effect
- Summary
- Abstract
- Description
- Claims
- Application Information
AI Technical Summary
Problems solved by technology
Method used
Image
Examples
Embodiment 1
[0032] A treatment process for waste tailings in a smelter, comprising the following steps:
[0033] (1) Electrolyte preparation: take a certain amount of dilute hydrochloric acid and add water and stir to prepare a hydrochloric acid solution with a pH value of 2 to 4, and add a certain amount of sodium chloride and hypochlorite to mix evenly;
[0034] (2) Liquid-solid mixing: Take a part of the electrolyte prepared in step (1) and mix it with the waste tailings of the smelter to make ore slurry, and the liquid-solid mixing ratio is 1.5:1;
[0035] (3) Transfer of the liquid-solid mixture: the ore slurry and the electrolyte formed in the step (2) are transported to the anode tank and the cathode tank of the electrolytic cell through pipelines respectively, and the liquid levels of the anode and the cathode are kept flush;
[0036] (4) Stir the mixture: Stir the anode electrolyzer where the electrolyte is placed in step (3) at a certain speed, turn on the power and feed compres...
Embodiment 2
[0043] A treatment process for waste tailings in a smelter, comprising the following steps:
[0044](1) Electrolyte preparation: take a certain amount of dilute hydrochloric acid and add water and stir to prepare a hydrochloric acid solution with a pH value of 2 to 4, and add a certain amount of sodium chloride and hypochlorite to mix evenly;
[0045] (2) Liquid-solid mixing: Take a part of the electrolyte prepared in step (1) and mix it with the waste tailings of the smelter to make ore slurry, and the liquid-solid mixing ratio is 2:1;
[0046] (3) Transfer of the liquid-solid mixture: the ore slurry and the electrolyte formed in the step (2) are transported to the anode tank and the cathode tank of the electrolytic cell through pipelines respectively, and the liquid levels of the anode and the cathode are kept flush;
[0047] (4) Stir the mixture: Stir the anode electrolyzer where the electrolyte is placed in step (3) at a certain speed, turn on the power and feed compressed...
PUM
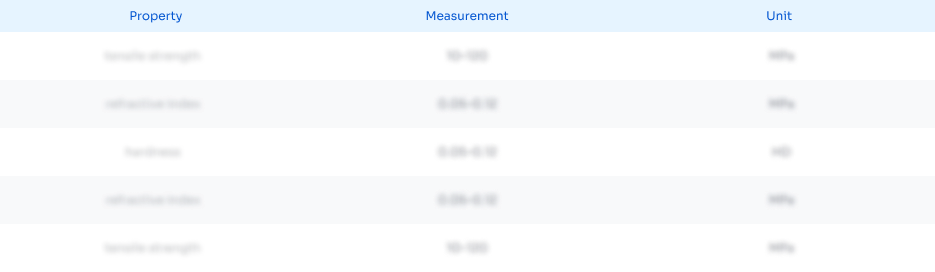
Abstract
Description
Claims
Application Information

- Generate Ideas
- Intellectual Property
- Life Sciences
- Materials
- Tech Scout
- Unparalleled Data Quality
- Higher Quality Content
- 60% Fewer Hallucinations
Browse by: Latest US Patents, China's latest patents, Technical Efficacy Thesaurus, Application Domain, Technology Topic, Popular Technical Reports.
© 2025 PatSnap. All rights reserved.Legal|Privacy policy|Modern Slavery Act Transparency Statement|Sitemap|About US| Contact US: help@patsnap.com