Hydraulically coupled electro-hydraulic brake system
A hydraulic braking and hydraulic coupling technology, which is applied in the direction of brakes, braking transmission devices, braking action starting devices, etc., can solve problems such as complex control algorithms, complex structures, and high motor performance requirements
- Summary
- Abstract
- Description
- Claims
- Application Information
AI Technical Summary
Problems solved by technology
Method used
Image
Examples
Embodiment Construction
[0071] see Figure 1 to Figure 8 Shown:
[0072] The present invention includes a human hydraulic cylinder 1, a booster hydraulic cylinder 2, a brake master cylinder 3, a brake pedal 4, a pedal stroke sensor 5, a booster motor 6, a booster transmission assembly 7, a normally open solenoid valve 8, a normally closed solenoid valve 9, Check valve A10, check valve B11, hydraulic control unit HCU12, hydraulic pressure sensor 13, electronic control unit ECU14:
[0073] The liquid outlet of the manpower hydraulic cylinder 1 is connected to the liquid inlet of the brake master cylinder 3 through a hydraulic pipeline, and the one-way valve A10 is arranged on the hydraulic pipeline between the manpower hydraulic cylinder 1 and the brake master cylinder 3, The normally open solenoid valve 8 is connected in parallel with the one-way valve A10 through the hydraulic pipeline, the brake pedal 4 is connected with the piston of the human hydraulic cylinder 1 through the pedal push rod 15, an...
PUM
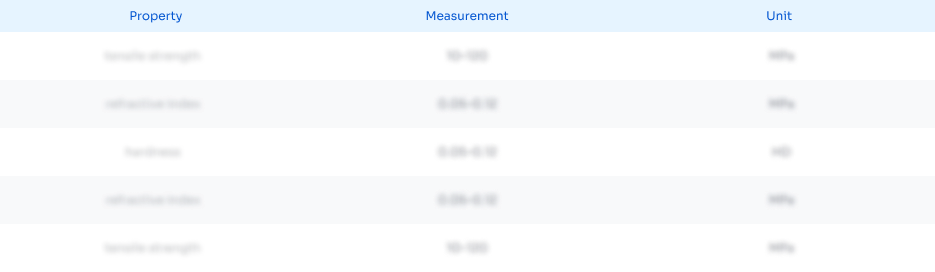
Abstract
Description
Claims
Application Information

- R&D
- Intellectual Property
- Life Sciences
- Materials
- Tech Scout
- Unparalleled Data Quality
- Higher Quality Content
- 60% Fewer Hallucinations
Browse by: Latest US Patents, China's latest patents, Technical Efficacy Thesaurus, Application Domain, Technology Topic, Popular Technical Reports.
© 2025 PatSnap. All rights reserved.Legal|Privacy policy|Modern Slavery Act Transparency Statement|Sitemap|About US| Contact US: help@patsnap.com