Composite metal oxide desulphurization agent and preparation method thereof
A technology of composite metal and desulfurizer, applied in chemical instruments and methods, separation methods, combustible gas purification, etc., can solve the problems of unstable oxygen content, carrier absorption, and high tail gas content, and achieves improved reaction efficiency, mild reaction conditions, The effect of improving the removal accuracy
- Summary
- Abstract
- Description
- Claims
- Application Information
AI Technical Summary
Problems solved by technology
Method used
Image
Examples
Embodiment 1
[0049] 1 Weigh 0.08mol of AlCl 3 .6H 2 O, 0.04mol of Cu(NO 3 ) 2 , 0.04mol MnCl 2 configured as Cu(NO 3 ) 2 The co-solution A with a mass fraction of 10% was poured into a 500mL three-neck flask for later use.
[0050] 2. Weigh again 0.13 mol of diethylenetriamine (EDTA), and configure it into 10% lye B for later use.
[0051] 3. Will be loaded with Cu(NO 3 ) 2 Place the three-necked flask of co-solution A of iso-salt in a water bath at 70°C, start stirring at 400r / min, add lye B to co-solution A drop by drop with a constant pressure dropping funnel, and the dropping speed is 1 drop / S, The dropping time is controlled at 1.5h, and the stirring is continued for 0.5h after the dropping, and the pH is controlled to be 10;
[0052] 4. After the dropwise addition was completed, continue to keep warm and stir for 1 hour, then stop the reaction, and place the obtained precipitate at the reaction temperature to age for 18 hours.
[0053] 5. After the aging is completed, add 1...
Embodiment 2
[0058] 1. Weigh 0.08mol of AlCl 3 .6H 2 O, 0.04mol of Cu(NO 3 ) 2 , 0.04mol ZnCl 2 configured as Cu(NO 3 ) 2 The co-solution A with a mass fraction of 10% was poured into a 500mL three-neck flask for later use.
[0059] 2. Weigh again 0.13mol DEA, and configure it into lye B with a mass fraction of 10%, and set it aside.
[0060] 3. Will be loaded with Cu(NO 3 ) 2 Place the three-neck flask of co-solution A of iso-salt in a water bath at 20°C, start stirring at 600r / min, add lye B to co-solution A drop by drop with a constant pressure dropping funnel, and the dropping speed is 3 drops / S, The dropping time is controlled at 1h, and the stirring is continued for 1h after the dropping is completed, and the pH is controlled to be 8;
[0061] 4. After the dropwise addition was completed, continue to heat and stir for 1 hour, then stop the reaction, and place the obtained precipitate at the reaction temperature to age for 36 hours.
[0062] 5. After the aging is completed, ...
Embodiment 3
[0067] 1. Weigh 0.08mol of AlCl 3 .6H 2 O, 0.04mol of Cu(NO 3 ) 2 , 0.04mol FeCl 3 configured as Cu(NO 3 ) 2 The co-solution A with a mass fraction of 10% was poured into a 500mL three-neck flask for later use.
[0068] 2. Weigh again 0.146 mol of diethylenetriamine (EDTA), configure it into lye B with a mass fraction of 10%, and set aside.
[0069] 3. Will be loaded with Cu(NO 3 ) 2 Place the three-necked flask of co-solution A of iso-salt in a water bath at 70°C, start stirring at 200r / min, add lye B to co-solution A drop by drop with a constant pressure dropping funnel, and the dropping speed is 3 drops / S, The dropping time is controlled at 1.5h, and the stirring is continued for 0.5h after the dropping, and the pH is controlled to be 9;
[0070] 4. After the dropwise addition was completed, continue to heat and stir for 1 hour, then stop the reaction, and place the obtained precipitate at the reaction temperature to age for 36 hours.
[0071]5. After the aging is...
PUM
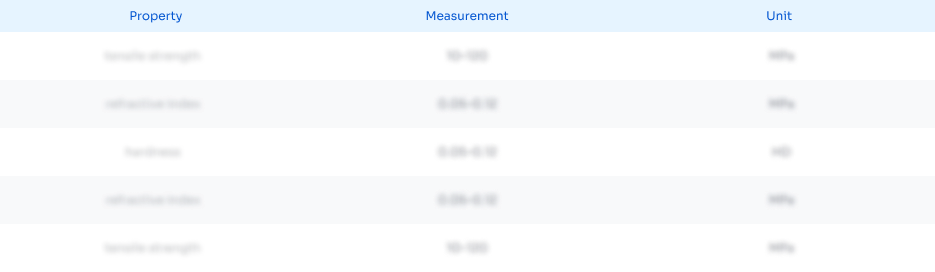
Abstract
Description
Claims
Application Information

- R&D Engineer
- R&D Manager
- IP Professional
- Industry Leading Data Capabilities
- Powerful AI technology
- Patent DNA Extraction
Browse by: Latest US Patents, China's latest patents, Technical Efficacy Thesaurus, Application Domain, Technology Topic, Popular Technical Reports.
© 2024 PatSnap. All rights reserved.Legal|Privacy policy|Modern Slavery Act Transparency Statement|Sitemap|About US| Contact US: help@patsnap.com