A LED flip chip and a manufacturing method thereof
A flip-chip and manufacturing method technology, applied in electrical components, circuits, semiconductor devices, etc., can solve problems such as low reflectivity of mirrors, restricting the quality of flip-chip LED chips, limitations in light absorption, and reflectivity, etc. Light output efficiency, improve photoelectric conversion efficiency, good heat dissipation effect
- Summary
- Abstract
- Description
- Claims
- Application Information
AI Technical Summary
Problems solved by technology
Method used
Examples
Embodiment 1
[0037] A method for manufacturing an LED flip chip, comprising the steps of:
[0038] A. A substrate is provided, the substrate is a sapphire substrate, and an N-type gallium nitride layer, a multi-quantum well layer and a P-type gallium nitride layer are sequentially formed on the substrate;
[0039] B. forming an ohmic contact layer on the surface of the substrate and patterning it to expose the p-type gallium nitride layer;
[0040] C. Forming a mirror dielectric layer on the ohmic contact layer and patterning it to expose the P-type gallium nitride layer and part of the ohmic contact layer;
[0041] D. forming a mirror metal layer, the mirror metal layer covering the mirror dielectric layer and the exposed ohmic contact layer;
[0042] E. Etching the exposed P-type gallium nitride layer and quantum well layer to form an N electrode contact hole;
[0043] F, forming an isolation layer, the isolation layer covers the mirror metal layer and the sidewall of the N electrode c...
Embodiment 2
[0061] The difference between this embodiment and the above-mentioned embodiment 1 is that the material of the reflector metal layer is a combination of Ni / Ag / Ti / Pt / Au / W, and its thickness ratio is 5:0.8:3:0.03:0.05 :1.
[0062] The material of the N electrode is a combination of Cr / Al / Ti / Pt / Au / Sn / Ag, and its thickness ratio is 3.5:2.5:1:0.02:0.09:0.9.
[0063] The material of the P electrode is a combination of Ni / Au / Cr / Pt / Au / Sn / W, and its thickness ratio is 2.5:0.05:1.5:0.04:0.06:1.
Embodiment 3
[0065] The difference between this embodiment and the above-mentioned embodiment 1 is that the material of the reflector metal layer is a combination of Ni / Ag / Ti / Pt / Au / W, and its thickness ratio is 6:1:4:0.04:0.06 :1.
[0066] The material of the N electrode is a combination of Cr / Al / Ti / Pt / Au / Sn / Ag, and its thickness ratio is 4:3:1:0.03:0.1:1.
[0067] The material of the P electrode is a combination of Ni / Au / Cr / Pt / Au / Sn / W, and its thickness ratio is 3:0.06:2:0.05:0.07:1.
PUM
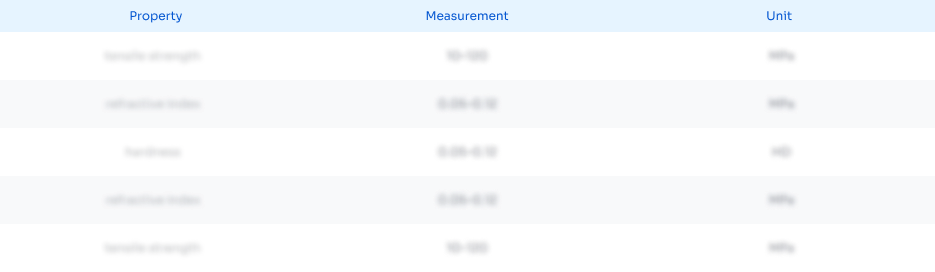
Abstract
Description
Claims
Application Information

- R&D
- Intellectual Property
- Life Sciences
- Materials
- Tech Scout
- Unparalleled Data Quality
- Higher Quality Content
- 60% Fewer Hallucinations
Browse by: Latest US Patents, China's latest patents, Technical Efficacy Thesaurus, Application Domain, Technology Topic, Popular Technical Reports.
© 2025 PatSnap. All rights reserved.Legal|Privacy policy|Modern Slavery Act Transparency Statement|Sitemap|About US| Contact US: help@patsnap.com