High-performance abrasion-resistant bearing and manufacturing technology thereof
A technology of wear-resistant bearings and manufacturing processes, which is applied in the direction of bearings, bearing cooling, bearing components, etc., and can solve the problem of low impact fatigue performance, low ability to withstand vibration and impact loads, high frequency and long life without lubrication, and affect the normal operation of butterfly valves. To improve the ability to withstand vibration and impact loads, to use safely and conveniently, and to maintain the effect of self-lubricating function
- Summary
- Abstract
- Description
- Claims
- Application Information
AI Technical Summary
Problems solved by technology
Method used
Image
Examples
Embodiment 1
[0031] Embodiment 1: as figure 1 As shown, the present invention provides a technical solution for the manufacture of high-performance wear-resistant bearings. The high-performance wear-resistant bearings are made of the following raw materials in parts by weight: 100 parts of chromium steel, 5 parts of magnesium powder, 6 parts of aluminum powder, copper 8 parts of powder, 5 parts of glass fiber, 15 parts of epoxy resin, 8 parts of polytetrafluoroethylene, 3 parts of carbon fiber, 3 parts of graphite, 0.75 parts of silicon barium calcium, 1.5 parts of metal toughening agent and 0.75 parts of curing agent.
[0032] According to above-mentioned technical scheme, comprise the following steps:
[0033] S1. Pour the chromium steel into a grinder, grind it into powder, add an appropriate amount of water to obtain a 250-mesh powder, and then put it into a blender;
[0034] S2. Put magnesium powder, aluminum powder, copper powder, glass fiber wire, epoxy resin, polytetrafluoroethyle...
Embodiment 2
[0042] Embodiment 2: as figure 1As shown, the high-performance wear-resistant bearing is made of the following raw materials in parts by weight: 90 parts of chrome steel, 3 parts of magnesium powder, 5 parts of aluminum powder, 5 parts of copper powder, 3 parts of glass fiber filaments, 10 parts of epoxy resin, 5 parts of polytetrafluoroethylene, 2 parts of carbon fiber, 2 parts of graphite, 0.5 part of silicon barium calcium, 1 part of metal toughening agent and 0.5 part of curing agent.
[0043] According to above-mentioned technical scheme, comprise the following steps:
[0044] S1. Pour the chromium steel into a grinder, grind it into powder, add an appropriate amount of water to obtain a 250-mesh powder, and then put it into a blender;
[0045] S2. Put magnesium powder, aluminum powder, copper powder, glass fiber filaments, epoxy resin, polytetrafluoroethylene, carbon fiber filaments, graphite and silicon barium calcium into a mixer, mix at 1100 rpm for 5 minutes, add me...
Embodiment 3
[0053] Embodiment 3: as figure 1 As shown, the high-performance wear-resistant bearing is made of the following raw materials in parts by weight: 110 parts of chrome steel, 5 parts of magnesium powder, 7 parts of aluminum powder, 10 parts of copper powder, 10 parts of glass fiber filaments, 20 parts of epoxy resin, 10 parts of polytetrafluoroethylene, 5 parts of carbon fiber filaments, 4 parts of graphite, 1 part of silicon barium calcium, 2 parts of metal toughening agent and 1 part of curing agent.
[0054] According to above-mentioned technical scheme, comprise the following steps:
[0055] S1. Pour the chromium steel into a grinder, grind it into powder, add an appropriate amount of water to obtain a 250-mesh powder, and then put it into a blender;
[0056] S2. Put magnesium powder, aluminum powder, copper powder, glass fiber wire, epoxy resin, polytetrafluoroethylene, carbon fiber wire, graphite and silicon-barium-calcium into the mixer, mix at 1100 rpm for 8 minutes, ad...
PUM
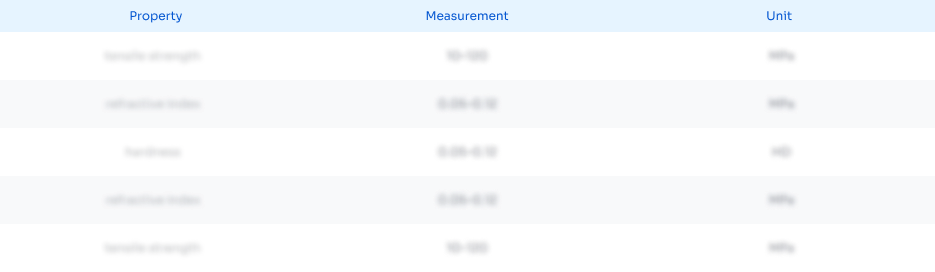
Abstract
Description
Claims
Application Information

- R&D
- Intellectual Property
- Life Sciences
- Materials
- Tech Scout
- Unparalleled Data Quality
- Higher Quality Content
- 60% Fewer Hallucinations
Browse by: Latest US Patents, China's latest patents, Technical Efficacy Thesaurus, Application Domain, Technology Topic, Popular Technical Reports.
© 2025 PatSnap. All rights reserved.Legal|Privacy policy|Modern Slavery Act Transparency Statement|Sitemap|About US| Contact US: help@patsnap.com