Preparation process of novel mold material for extrusion twist drill
A technology of mold material and preparation process, which is applied in the field of preparation of mold materials for new extruded twist drills, can solve problems affecting the quality of stamping parts, affecting the service life of molds, wear and other problems, and achieves improved hardness and toughness and extended service life , the effect of increasing the tempering temperature
- Summary
- Abstract
- Description
- Claims
- Application Information
AI Technical Summary
Problems solved by technology
Method used
Examples
Embodiment 1
[0024] The invention provides a preparation process of a new mold material for extruding twist drills. The main chemical composition of the mold material is composed of C 1.48-1.55, Cr 12-13, Mo 0.45-0.50 and V 0.19-0.22. The preparation process includes heat treatment and nitriding treatment, and the heat treatment process steps are as follows:
[0025] (1) First put the mold into the furnace and use high-frequency heating. After heating to 1150~1200°C, oil cooling or graded cooling;
[0026] (2) Then temper the mold obtained after step (1) at 550~560°C for 5~6 times.
[0027] According to the above-mentioned preparation process of the mold material for the new extruded twist drill, the nitriding treatment is to carry out nitriding at 520~560°C when the nitrogen ratio is 50% after the mold workpiece is quenched and tempered with oil. deal with.
Embodiment 2
[0029] The invention provides a preparation process of a new mold material for extruding twist drills. The main chemical composition of the mold material is composed of C 1.5, Cr 12.5, Mo 0.45 and V 0.22. Its preparation process includes heat treatment and nitriding treatment , the heat treatment process steps are as follows:
[0030] (1) First put the mold into the furnace and use high-frequency heating. After heating to 1170°C, it is oil-cooled or graded-cooled;
[0031] (2) Then temper the mold obtained after step (1) at 550 for 5~6 times.
[0032] According to the above-mentioned preparation process of the mold material for the new extruded twist drill, the nitriding treatment is to carry out the nitriding treatment at 550° C. after the mold workpiece is quenched and tempered by oil, and the nitrogen ratio is 50%.
Embodiment 3
[0034] The invention provides a preparation process of a new mold material for extruding twist drills. The main chemical composition of the mold material is composed of C 1.48, Cr 13, Mo 0.45 and V 0.22. Its preparation process includes heat treatment and nitriding treatment , the heat treatment process steps are as follows:
[0035] (1) First put the mold into the furnace and use high-frequency heating. After heating to 1200°C, it is oil-cooled or graded-cooled;
[0036] (2) Then temper the mold obtained after step (1) at 550°C for 5 times.
[0037] According to the above-mentioned preparation process of the mold material for the new extruded twist drill, the nitriding treatment is to carry out the nitriding treatment at 540° C. after the mold workpiece is quenched and tempered by oil, and the nitrogen ratio is 50%.
PUM
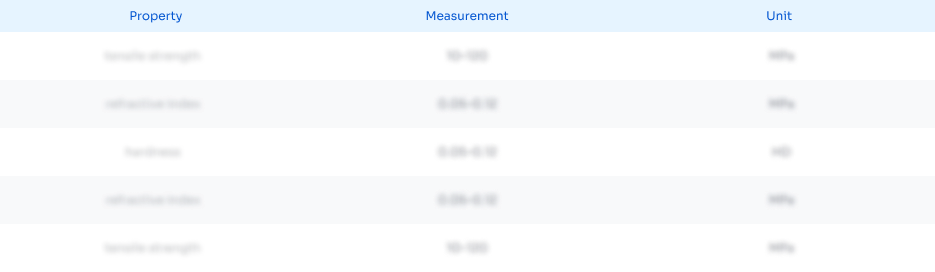
Abstract
Description
Claims
Application Information

- R&D
- Intellectual Property
- Life Sciences
- Materials
- Tech Scout
- Unparalleled Data Quality
- Higher Quality Content
- 60% Fewer Hallucinations
Browse by: Latest US Patents, China's latest patents, Technical Efficacy Thesaurus, Application Domain, Technology Topic, Popular Technical Reports.
© 2025 PatSnap. All rights reserved.Legal|Privacy policy|Modern Slavery Act Transparency Statement|Sitemap|About US| Contact US: help@patsnap.com