In-situ microfiber reinforced MC nylon composite material preparation method
A nylon composite material, in-situ microfiber technology
- Summary
- Abstract
- Description
- Claims
- Application Information
AI Technical Summary
Problems solved by technology
Method used
Examples
Embodiment 1
[0026] The preparation method for preparing PP / PA6 in-situ microfibrillation composite material provided by the present invention is carried out according to the following process steps and conditions:
[0027] (1) Put caprolactam (CL) into melting pot A, raise the temperature to 127°C, set the pressure to normal pressure, and melt it;
[0028] (2) Add the auxiliary material catalyst sodium hydroxide (NaOH) into the melt kettle A, and carry out vacuum dehydration of the molten raw materials in the negative pressure dehydration system, set the dehydration temperature to 127°C, and the dehydration (absolute) pressure to be less than 5mmHg;
[0029] (3) Add the auxiliary material curing agent toluene-2,4-diisocyanate (TDI) into the melt kettle A, continue vacuum dehydration in the negative pressure dehydration system, set the dehydration temperature to 127°C, and the dehydration (absolute) pressure is less than 5mmHg;
[0030] (4) Start the nitrogen charging switch, input the ra...
Embodiment 2
[0038] The preparation method for preparing PP / PA6 in-situ microfibrillation composite material provided by the present invention is carried out according to the following process steps and conditions:
[0039] (1) Put caprolactam (CL) into melting pot A, raise the temperature to 120°C, set the pressure to normal pressure, and melt it;
[0040] (2) Add the auxiliary material catalyst sodium hydroxide (NaOH) into the melt kettle A, and carry out vacuum dehydration of the molten raw materials in the negative pressure dehydration system, set the dehydration temperature to 120°C, and the dehydration (absolute) pressure to be less than 5mmHg;
[0041] (3) Add the auxiliary material curing agent toluene-2,4-diisocyanate (TDI) into the melt kettle A, continue vacuum dehydration in the negative pressure dehydration system, set the dehydration temperature to 120°C, and the dehydration (absolute) pressure is less than 5mmHg;
[0042] (4) Start the nitrogen charging switch, input the ra...
Embodiment 3
[0050] The preparation method for preparing PP / PA6 in-situ microfibrillation composite material provided by the present invention is carried out according to the following process steps and conditions:
[0051] (1) Put caprolactam (CL) into melting pot A, raise the temperature to 135°C, set the pressure to normal pressure, and melt it;
[0052] (2) Add the auxiliary material catalyst sodium hydroxide (NaOH) into the melt kettle A, and carry out vacuum dehydration of the molten raw materials in the negative pressure dehydration system, set the dehydration temperature to 135°C, and the dehydration (absolute) pressure to be less than 5mmHg;
[0053] (3) Add the auxiliary material curing agent toluene-2,4-diisocyanate (TDI) into the melt kettle A, continue vacuum dehydration in the negative pressure dehydration system, set the dehydration temperature to 135 ° C, and the dehydration (absolute) pressure is less than 5mmHg;
[0054] (4) Start the nitrogen charging switch, input the ...
PUM
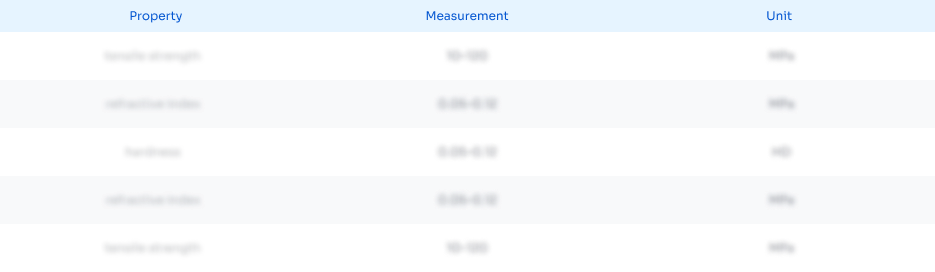
Abstract
Description
Claims
Application Information

- Generate Ideas
- Intellectual Property
- Life Sciences
- Materials
- Tech Scout
- Unparalleled Data Quality
- Higher Quality Content
- 60% Fewer Hallucinations
Browse by: Latest US Patents, China's latest patents, Technical Efficacy Thesaurus, Application Domain, Technology Topic, Popular Technical Reports.
© 2025 PatSnap. All rights reserved.Legal|Privacy policy|Modern Slavery Act Transparency Statement|Sitemap|About US| Contact US: help@patsnap.com