Special smelting furnace
A smelting furnace and furnace cover technology, applied in the field of smelting furnaces, can solve the problems of environmental pollution and unfavorable large-scale production of aluminum alloys.
- Summary
- Abstract
- Description
- Claims
- Application Information
AI Technical Summary
Problems solved by technology
Method used
Image
Examples
Embodiment Construction
[0021] In order to make the object, technical solution and advantages of the present invention clearer, the implementation manner of the present invention will be further described in detail below in conjunction with the accompanying drawings.
[0022] Embodiments of the present invention provide a special melting furnace, such as figure 1 As shown, the special melting furnace includes: a shell 1, a heating assembly 2, a crucible 3, a driving assembly 4, a stirring blade 5 and a furnace cover 6, the crucible 3 is arranged in the shell 1, and the furnace cover 6 is installed on the shell 1 , the transmission shaft of the driving assembly 4 passes through the furnace cover 6, the stirring blade 5 is located in the crucible 3 and is installed on the transmission shaft of the driving assembly 4, the special melting furnace also includes: an evaporator 7 and a water inlet pipe 8, combined figure 2 As shown, the evaporator 7 includes: an evaporator housing 7a, an evaporator copper ...
PUM
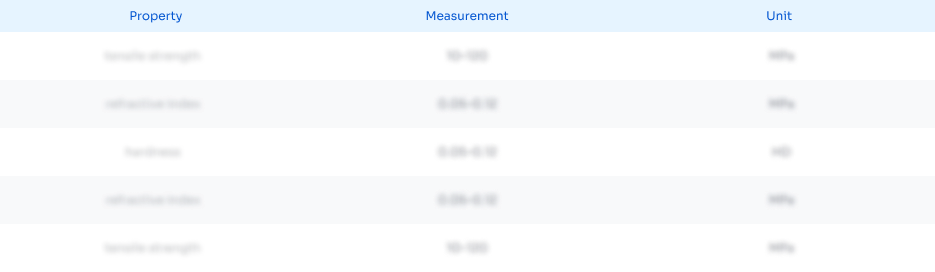
Abstract
Description
Claims
Application Information

- R&D
- Intellectual Property
- Life Sciences
- Materials
- Tech Scout
- Unparalleled Data Quality
- Higher Quality Content
- 60% Fewer Hallucinations
Browse by: Latest US Patents, China's latest patents, Technical Efficacy Thesaurus, Application Domain, Technology Topic, Popular Technical Reports.
© 2025 PatSnap. All rights reserved.Legal|Privacy policy|Modern Slavery Act Transparency Statement|Sitemap|About US| Contact US: help@patsnap.com