Porous biomass carbon electrode material derived from wheat straws and preparation method thereof
A technology of biomass charcoal and wheat straw, which is applied in the manufacture of hybrid capacitor electrodes and hybrid/electric double-layer capacitors, can solve the problems of waste of resources, human health threats, toxic and harmful substances in straw haze, etc., and reduce environmental pollution. Effect
- Summary
- Abstract
- Description
- Claims
- Application Information
AI Technical Summary
Problems solved by technology
Method used
Image
Examples
Embodiment 1
[0024] ① The raw material wheat straw is cleaned, dried and crushed into powder, and sieved with a 200-mesh sieve. Then mix 10g of citric acid and 10g of wheat straw powder, add 100mL of ionized water, and ultrasonicate for 30 minutes to completely dissolve the citric acid, then add 2.5g of NaH 2 PO 4 , magnetically stirred until a straw slurry was formed.
[0025] ② Freeze the obtained straw slurry and dry it with a freeze dryer, then carbonize it in a high-temperature tube furnace in a flowing Ar atmosphere, raise the temperature to 800°C and keep it warm for 2 hours, and wash the calcined product with dilute hydrochloric acid and deionized water until the pH is equal to 7 , to obtain biochar material after drying.
[0026] ③ Mix 0.5 g of the biochar material prepared in step (2) with 1.5 g of KOH, ultrasonically mix in 10 mL of water for 30 minutes, and dry the resulting mixture at 60° C. The dried mixed samples were heated to 800 °C in an Ar atmosphere and kept for 2 h....
Embodiment 2
[0030] ① The raw material wheat straw is cleaned, dried and crushed into powder, and sieved with a 200-mesh sieve. Then mix 8g of citric acid and 8g of wheat straw powder, add 50mL of ionized water, and ultrasonicate for 30 minutes to completely dissolve the citric acid, then add 2g of NaH 2 PO 4 , magnetically stirred until a straw slurry was formed.
[0031] ② Freeze the obtained straw slurry and dry it with a freeze dryer, then carbonize it in a high-temperature tube furnace in a flowing Ar atmosphere, raise the temperature to 800°C and keep it warm for 2 hours, and wash the calcined product with dilute hydrochloric acid and deionized water until the pH is equal to 7 , to obtain biochar material after drying.
[0032] ③ Mix 0.5 g of the biochar material prepared in step (2) with 2.5 g of KOH, ultrasonically mix in 10 mL of water for 30 minutes, and dry the resulting mixture at 60° C. The dried mixed samples were heated to 800 °C in an Ar atmosphere and kept for 2 h. Fin...
Embodiment 3
[0035] ① The raw material wheat straw is cleaned, dried and crushed into powder, and sieved with a 200-mesh sieve. Then mix 16g of citric acid and 16g of wheat straw powder, add 200mL of ionized water, and ultrasonicate for 30 minutes to completely dissolve the citric acid, then add 4g of NaH 2 PO 4 , magnetically stirred until a straw slurry was formed.
[0036] ② Freeze the obtained straw slurry and dry it with a freeze dryer, then carbonize it in a high-temperature tube furnace in a flowing Ar atmosphere, raise the temperature to 800°C and keep it warm for 2 hours, and wash the calcined product with dilute hydrochloric acid and deionized water until the pH is equal to 7 , to obtain biochar material after drying.
[0037] ③ Mix 0.5 g of the biochar material prepared in step (2) with 3.5 g of NaOH, ultrasonically mix in 10 mL of water for 30 minutes, and dry the resulting mixture at 60° C. The dried mixed samples were heated to 800 °C in an Ar atmosphere and kept for 2 h. ...
PUM
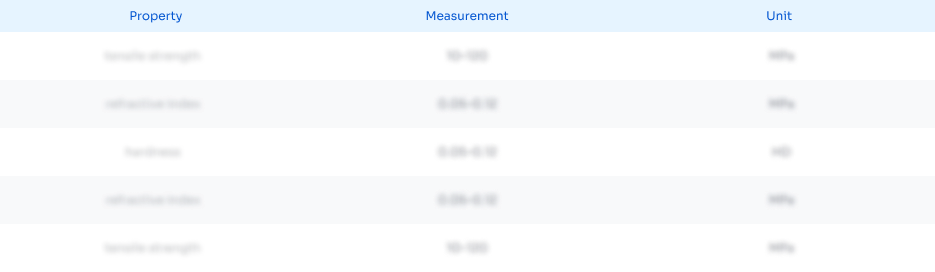
Abstract
Description
Claims
Application Information

- R&D
- Intellectual Property
- Life Sciences
- Materials
- Tech Scout
- Unparalleled Data Quality
- Higher Quality Content
- 60% Fewer Hallucinations
Browse by: Latest US Patents, China's latest patents, Technical Efficacy Thesaurus, Application Domain, Technology Topic, Popular Technical Reports.
© 2025 PatSnap. All rights reserved.Legal|Privacy policy|Modern Slavery Act Transparency Statement|Sitemap|About US| Contact US: help@patsnap.com