Method for recovering rubidium, caesium, aluminum and potassium from mixed alum by-produced during extraction of lithium from lithionite
A by-product, lepidolite technology, which is applied in the field of recycling rare metals, achieves the effects of high comprehensive utilization rate, reduced production cost, and reduced production cost
- Summary
- Abstract
- Description
- Claims
- Application Information
AI Technical Summary
Problems solved by technology
Method used
Image
Examples
Embodiment 1
[0022] Embodiment 1: The concentration involved in the embodiment is the mass concentration.
[0023] Get 2.5 tons of mixed alum as a by-product of lepidolite extraction of lithium, and the mixed alum is a mixture containing potassium alum, rubidium alum, and cesium alum; according to the mass ratio of mixed alum and water, add water to 25 cubic meters of In the slurry mixing tank, add the additive CaO, react at a reaction temperature of 70°C for 60 minutes, and the pH of the reaction end point is 6; perform liquid-solid separation to obtain solid slag containing aluminum hydroxide and calcium sulfate and rubidium, cesium, and potassium. Sulfate solution; the obtained solid slag of aluminum hydroxide and calcium sulfate and 30% sulfuric acid are reacted at 70°C for 80 minutes at a mass ratio of 1:2, and the pH at the end of the reaction is 2.5; liquid-solid separation is carried out to obtain Aluminum sulfate solution; the aluminum sulfate solution is evaporated and concentrat...
Embodiment 2
[0025] The technical methods in the following examples are all the same as in Example 1 except for the following descriptions.
[0026] Take 3.0 tons of mixed alum as a by-product of lepidolite extraction of lithium, add water in a 25 cubic slurry tank according to the mass ratio of mixed alum and water of 1:7, and add additive CaO, and react at a reaction temperature of 80°C 90min; Reaction end point pH=8; Carry out liquid-solid separation, obtain the solid slag containing aluminum hydroxide and calcium sulfate and the sulfate solution containing rubidium, cesium, potassium; % sulfuric acid, according to the mass ratio of 1:3.5, reacted at 80°C for 80 minutes, and the pH of the reaction end point was 1.5; carried out liquid-solid separation to obtain aluminum sulfate solution; evaporated and concentrated the aluminum sulfate solution to Al 2 o 3 After the concentration is 190g / L, carry out cooling crystallization, and the crystallization temperature is controlled at 35±2°C. ...
PUM
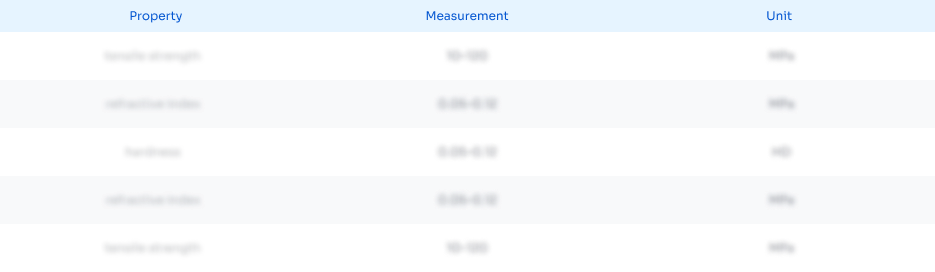
Abstract
Description
Claims
Application Information

- R&D
- Intellectual Property
- Life Sciences
- Materials
- Tech Scout
- Unparalleled Data Quality
- Higher Quality Content
- 60% Fewer Hallucinations
Browse by: Latest US Patents, China's latest patents, Technical Efficacy Thesaurus, Application Domain, Technology Topic, Popular Technical Reports.
© 2025 PatSnap. All rights reserved.Legal|Privacy policy|Modern Slavery Act Transparency Statement|Sitemap|About US| Contact US: help@patsnap.com